3D-принтер:3D-печать/Часть четвертая — Техники: различия между версиями
Myagkij (обсуждение | вклад) Нет описания правки |
Myagkij (обсуждение | вклад) Нет описания правки |
||
(не показаны 2 промежуточные версии этого же участника) | |||
Строка 10: | Строка 10: | ||
[[File:processes_stereolithography.png|center]] | [[File:processes_stereolithography.png|center]] | ||
Стереолитографию (SL) многие считают самой первой 3D-печатной техникой, но она была, скорее, первой 3D-печатной техникой, из которой получилось извлечь коммерческую выгоду. SL – это процесс, при котором лазер воздействует на жидкую полимерную смолу, в результате чего она запекается и крепнет, тем самым обретая определенную форму. Это сложный процесс, но если вкратце, то фотополимерная смола помещается в емкость, внутри которой находится подвижная (перемещающаяся вверх и вниз) платформа. Затем поверхность этого смоляного «пруда» обрабатывается лазерным лучом — он перемещается из стороны в сторону согласно данным по осям X и Y, указанным в STL-файле, который 3D-принтер использует для создания объекта. В результате в том месте, где луч соприкасается со смолой, она затвердевает. Когда слой будет выполнен, платформа внутри емкости опускается на одну ступень вниз (т.е. по оси Z), и лазер начинает создавать новый слой. Это продолжается до тех пор, пока объект не будет готов, после чего платформа вытаскивается из емкости, чтобы достать объект. | |||
Из-за особенностей этой техники некоторым частям создаваемого объекта требуются опоры — особенно тем, где есть какие-нибудь вырезы или выступы. Позднее эти опоры нужно будет удалить вручную. | Из-за особенностей этой техники некоторым частям создаваемого объекта требуются опоры — особенно тем, где есть какие-нибудь вырезы или выступы. Позднее эти опоры нужно будет удалить вручную. | ||
Строка 21: | Строка 21: | ||
[[File:processes_dlp1.png|center]] | [[File:processes_dlp1.png|center]] | ||
DLP (digital light processing, т.е. «цифровая светодиодная проекция») — это техника, похожая на стереолитографию в том, что в ней тоже используются фотополимеры. Главное отличие — в источнике света. DLP использует более традиционный источник света (вроде дуговой лампы), а также жидко-кристаллическую панель или прибор с деформируемым зеркалом (deformable mirror device или просто DMD), который воздействует сразу на всю поверхность емкости с фотополимером. Как правило, это позволяет создавать объект быстрее, чем при помощи стереолитографии. | |||
Кроме того, как и | Кроме того, как и SL, DLP позволяет делать объекты более высокой точности и с отличным разрешением, но для этой техники требуется и та же постобработка — удаление опор и повторное отверждение. Впрочем, одним из преимуществ DLP по сравнению с SL является то, что для создания объекта требуется лишь одна неглубокая емкость с фотополимером, а это, как правило, позволяет экономить расходный материал. | ||
==Лазерное спекание / лазерное плавление / SLS== | ==Лазерное спекание / лазерное плавление / SLS== | ||
[[File:processes_sintering.png]] | [[File:processes_sintering.png|center]] | ||
Лазерное спекание и лазерное плавление — это взаимозаменяемые термины, обозначающие 3D-печатный процесс, при котором объект создается путем обработки лазером порошкового материала. В 3D-принтер загружают файл с данными о создаваемом объекте, а лазер, беря за основу эти данные, «скользит» по поверхности исходного материала — порошка, утрамбованного в специальной емкости. Когда лазер взаимодействует с поверхностью, частицы порошкового материала спекаются/сплавляются друг с другом, обретая твердую форму. После создания слоя емкость с порошком опускается на одну ступень вниз, а сверху по ней проезжает валик — он утрамбовывает и подсыпает порошок перед тем, как лазер начнет создавать новый слой, попутно скрепляя его с предыдущим. | |||
Платформа с порошком полностью запечатана, т.к. для успешного спекания необходимо, чтобы исходный материал был определенной температуры. По завершении процесса емкость с порошком вынимается, лишний порошок убирается, и в итоге остается лишь напечатанный объект. Одним из ключевых преимуществ этой техники является то, что порошок служит в качестве опорного элемента для разного рода выступов и свесов, избавляя от необходимости проектировать опоры перед печатью объекта. Следовательно, при помощи лазерного спекания можно создавать сложные объекты, которые невозможно создать при помощи других техник. | Платформа с порошком полностью запечатана, т.к. для успешного спекания необходимо, чтобы исходный материал был определенной температуры. По завершении процесса емкость с порошком вынимается, лишний порошок убирается, и в итоге остается лишь напечатанный объект. Одним из ключевых преимуществ этой техники является то, что порошок служит в качестве опорного элемента для разного рода выступов и свесов, избавляя от необходимости проектировать опоры перед печатью объекта. Следовательно, при помощи лазерного спекания можно создавать сложные объекты, которые невозможно создать при помощи других техник. | ||
Строка 35: | Строка 35: | ||
Впрочем, у этой техники есть и недостатки — из-за высокой температуры, необходимой для лазерного спекания, очень много времени может понадобиться на охлаждение. Более того, давней проблемой лазерного спекания является пористость на итоговом объекте. И хотя в последнее время на этом фронте видны значительные улучшения, в некоторых случаях для улучшения механических характеристик объекта по-прежнему используют пропитку другим материалом. | Впрочем, у этой техники есть и недостатки — из-за высокой температуры, необходимой для лазерного спекания, очень много времени может понадобиться на охлаждение. Более того, давней проблемой лазерного спекания является пористость на итоговом объекте. И хотя в последнее время на этом фронте видны значительные улучшения, в некоторых случаях для улучшения механических характеристик объекта по-прежнему используют пропитку другим материалом. | ||
При лазерном спекании/плавлении можно использовать пластик и металлы, но сплавление металла требует гораздо более мощного лазера и более высоких температур. Объекты, создаваемые при помощи этого метода, гораздо прочнее, чем создаваемые посредством | При лазерном спекании/плавлении можно использовать пластик и металлы, но сплавление металла требует гораздо более мощного лазера и более высоких температур. Объекты, создаваемые при помощи этого метода, гораздо прочнее, чем создаваемые посредством SL и DLP, но есть и недостатки — более низкие качество поверхности и точность. | ||
==Экструзия / FDM / FFF== | ==Экструзия / FDM / FFF== | ||
Строка 41: | Строка 41: | ||
[[File:processes_FFF-Extrusion.png|center]] | [[File:processes_FFF-Extrusion.png|center]] | ||
Самым распространенным (и узнаваемым) 3D-печатным процессом является экструзия термопластического материала. Наиболее известное название этой техники — это | Самым распространенным (и узнаваемым) 3D-печатным процессом является экструзия термопластического материала. Наиболее известное название этой техники — это FDM (т.е. fused deposition modelling или «моделирование методом наплавления»), которое является и коммерческим наименованием, зарегистрированным Stratasys (компанией, которая изначально разработала эту технику). Технология FDM появилась на свет еще в начале 90-ых, но используется и по сей день, причем даже на промышленном уровне. Большая часть 3D-принтеров начального уровня, появившихся после 2009 года, используют похожую технику — она именуется, как правило, freeform fabrication или FFF (что значит «изготовление объектов произвольной формы) и представляет собой упрощенную вариацию FDM, потому что патенты на эту технологию по-прежнему принадлежат Stratasys. Первые RepRap и их последователи — и коммерческие версии, и версии с открытым кодом — тоже используют метод экструзии. Однако после иска о нарушении патента, поданного Stratasys против Afinia, то, как будет развиваться рынок 3D-принтеров начального уровня, теперь под вопросом, т.к. все эти машины теперь под угрозой иска со стороны Stratasys. | ||
Суть техники в следующем: пластиковая нить пропускается через экструдер, где нагревается, а затем размещается на платформе — слой за слоем, согласно 3D-данным в файле, | Суть техники в следующем: пластиковая нить пропускается через экструдер, где нагревается, а затем размещается на платформе — слой за слоем, согласно 3D-данным в файле, «скормленном» 3D-принтеру. Будучи отложенным, пластик застывает и скрепляется с предыдущим слоем. | ||
Компания | Компания Stratasys разработала для FDM несколько фирменных материалов, пригодных для производства объектов на промышленном уровне. Диапазон материалов для 3D-принтеров начального уровня более узок, но продолжает расширяться. Самыми распространенными материалами для начальных FFF-принтеров в данный момент являются ABS и PLA. | ||
Объектам, создаваемым при помощи | Объектам, создаваемым при помощи FDM и FFF, требуются опорные элементы — для свисающих частей. В FDM для этих опор используется еще один, водорастворимый материал, который после завершения печати (относительно легко) смывается водой. Впрочем, опоры можно удалить и вручную, просто отломив их от объекта. Для FFF-принтеров начального уровня опорные структуры (или их недостаточное количество) всегда были проблемой, однако, поскольку устройства эволюционируют, улучшаются и оснащаются двойными экструзионными головками, она становится все менее болезненной. | ||
Что касается создаваемых объектов, | Что касается создаваемых объектов, FDM от Stratasys – это довольно точный и аккуратный процесс и, к тому же, относительно дружественный к использованию дома и в офисе. Правда, после печати объекта может потребоваться долгая постобработка. Впрочем, как можно ожидать, на начальном уровне (т.е. при использовании FFF) объекты получаются менее точными, но ситуация постоянно улучшается. | ||
Если у создаваемого объекта сложная геометрия, то процесс может быть довольно долгим, и сцепление слоев друг с другом тоже может быть проблемой, в результате чего объект не всегда получается водонепроницаемым. Впрочем, эту проблему можно решить, например, при помощи ацетона. | Если у создаваемого объекта сложная геометрия, то процесс может быть довольно долгим, и сцепление слоев друг с другом тоже может быть проблемой, в результате чего объект не всегда получается водонепроницаемым. Впрочем, эту проблему можно решить, например, при помощи ацетона. | ||
Строка 58: | Строка 58: | ||
[[File:processes_inkjet-binder.png|center]] | [[File:processes_inkjet-binder.png|center]] | ||
Впрыскивание связующего вещества (binder jetting). В данном случае впрыскиваемым материалом является связующее вещество — оно выборочно впрыскивается на емкость с порошком, чтобы сделать из него один слой. После этого емкость с порошком опускается на ступень ниже, а сверху на по ней пробегает валик (или пластина), который подсыпает в емкость еще порошка, а заодно утрамбовывает его перед следующим проходом впрыскивающей головки. Вещество из этой головки связывает предыдущий и следующий слои друг с другом. | |||
Преимуществом этой техники (как и у | Преимуществом этой техники (как и у SLS) является то, что объекту не нужны опорные элементы, т.к. в их роли выступает порошок. Кроме того, диапазон используемых материалов включает в себя керамику и еду. И еще одно важное преимущество — возможность раскрасить объект разными цветами, что осуществляется через добавление красителя в связующее вещество. | ||
Таким образом, такой | Таким образом, такой 3D-принтер создает практически готовый объект, но он получается не таким прочным, как при лазерном спекании, а для обеспечения долговечности требуется некоторая постобработка. | ||
[[File:processes_inkjet2.png|center]] | [[File:processes_inkjet2.png|center]] | ||
Впрыскивание материала (material jetting). В данном случае впрыскивается, собственно, сам материал (в жидком или расплавленном состоянии) — это происходит выборочно и из нескольких головок (одновременно с другими материалами). Как правило, эта технология использует жидкие фотополимеры, и после наложения нового слоя он подвергается воздействию ультрафиолетового света, благодаря чему отвердевает. | |||
Кроме того, в связи с тем, что этот метод позволяет одновременное использование сразу нескольких материалов, то и объект тоже можно сделать неоднородным — чтобы разные его части имели разные свойства и характеристики. Впрыскивание материала является очень аккуратным методом 3D-печати, позволяющим создавать точные объекты с очень гладкой поверхностью. | Кроме того, в связи с тем, что этот метод позволяет одновременное использование сразу нескольких материалов, то и объект тоже можно сделать неоднородным — чтобы разные его части имели разные свойства и характеристики. Впрыскивание материала является очень аккуратным методом 3D-печати, позволяющим создавать точные объекты с очень гладкой поверхностью. | ||
Строка 74: | Строка 74: | ||
[[File:processes_sdl.png|center]] | [[File:processes_sdl.png|center]] | ||
SDL – это 3D-печатная техника, разработанная компанией Mcor Technologies и ею же запатентованная. Есть соблазн сравнить эту технологию с LOM (т.е. с «изготовлением объектов при помощи ламинирования»), которую в 90-ых годах разработала компания Helisys, т.к. оба метода используют бумагу и послойное наложение. Впрочем, на этом сходства между ними заканчиваются. | |||
SDL создает объекты слой за слоем при помощи стандартной копировальной бумаги. Новый слой скрепляется с предыдущим посредством клея, который применяется выборочно в соответствии с 3D-данными из файла, загруженного в принтер. Это значит, что в местах, где будет, собственно, сам объект, клея будет добавляться много, а там, где будут опорные элементы — гораздо меньше, чтобы потом эти опорные элементы было проще удалить. | |||
После того, как механизм подачи бумаги | После того, как механизм подачи бумаги «скармливает» принтеру новый лист и помещает его поверх предыдущего листа с выборочно добавленным клеем, платформа поднимается вверх, к нагревательной пластине, после чего объект подвергается прессованию — оно должно обеспечить крепкую связь между двумя листами бумаги. Затем платформа возвращается к своей изначальной высоте, где карбид-вольфрамовое лезвие пробегается по контуру объекта, тем самым создавая края нового слоя. По завершении резки 3D-принтер накладывает новый слой клея и весь цикл начинается заново. | ||
[[File:processes_sdl-process.png|center]] | [[File:processes_sdl-process.png|center]] | ||
SDL – один из немногих 3D-печатных процессов, использующих палитру CMYK и благодаря этому способных создавать многоцветные объекты. А поскольку исходным материалом выступает обычная бумага, которой не требуется никакая постобработка, эти объекты полностью безопасны и экологически безвредны. Впрочем, по некоторым параметрам SDL все же проигрывает другим 3D-печатным техникам — в создании объектов со сложной геометрией и в том, что размер объектов ограничен размером исходного сырья. | |||
==EBM== | ==EBM== | ||
Строка 88: | Строка 88: | ||
[[File:processes_ebm.png|center]] | [[File:processes_ebm.png|center]] | ||
Электронно-лучевая плавка (electron beam melting или EBM) — это 3D-печатная техника, принадлежащая и разработанная шведской компанией Arcam. Она похожа на DMLS (т.е. на прямое лазерное спекание металлов) в том смысле, что обе технологии формируют объект из металлического порошка. Ключевое отличие — в источнике тепла. В технике EBM в его роли, как можно судить из названия, выступает электронный луч, а не лазер, в связи с чем процедура должна проводиться в условиях вакуума. | |||
EBM позволяет создавать изделия максимальной плотности из различных металлических сплавов, в результате чего этот метод успешно используется в медицинской промышленности, особенно для производства имплантов. Тем не менее, другие высокотехнологичные сектора (вроде авиакосмической и автомобильной промышленности) тоже поглядывают в сторону EBM. | |||
=См.также= | =См.также= | ||
{{ads}} | |||
=Внешние ссылки= | =Внешние ссылки= | ||
<references /> | <references /> | ||
{{Навигационная таблица/Телепорт}} | |||
[[Категория:3D-печать]] | [[Категория:3D-печать]] |
Текущая версия от 09:20, 7 мая 2022
Содержание | 3D-печать | Материалы для 3D-печати | Хитрости и советы | 3D-модели для 3D-принтера | Программное обеспечение | Неисправности |
3D-печать. Часть четвертая — Техники[1]
Стереолитография
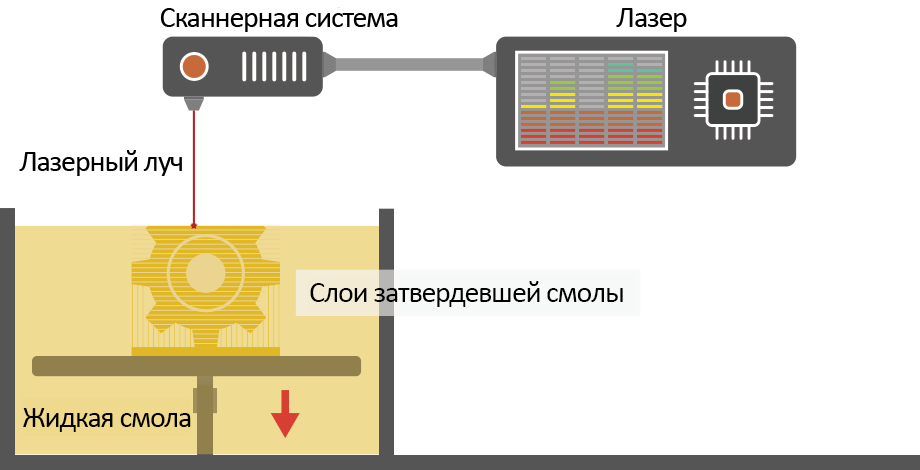
Стереолитографию (SL) многие считают самой первой 3D-печатной техникой, но она была, скорее, первой 3D-печатной техникой, из которой получилось извлечь коммерческую выгоду. SL – это процесс, при котором лазер воздействует на жидкую полимерную смолу, в результате чего она запекается и крепнет, тем самым обретая определенную форму. Это сложный процесс, но если вкратце, то фотополимерная смола помещается в емкость, внутри которой находится подвижная (перемещающаяся вверх и вниз) платформа. Затем поверхность этого смоляного «пруда» обрабатывается лазерным лучом — он перемещается из стороны в сторону согласно данным по осям X и Y, указанным в STL-файле, который 3D-принтер использует для создания объекта. В результате в том месте, где луч соприкасается со смолой, она затвердевает. Когда слой будет выполнен, платформа внутри емкости опускается на одну ступень вниз (т.е. по оси Z), и лазер начинает создавать новый слой. Это продолжается до тех пор, пока объект не будет готов, после чего платформа вытаскивается из емкости, чтобы достать объект.
Из-за особенностей этой техники некоторым частям создаваемого объекта требуются опоры — особенно тем, где есть какие-нибудь вырезы или выступы. Позднее эти опоры нужно будет удалить вручную. Впрочем, многим объектам, созданным с помощью стереолитографии, требуется и другая постобработка — очистка и отверждение. Причем для отверждения объект нужно подвергнуть воздействию сильного света, и это можно осуществить, например, в аппарате вроде духовки.
Стереолитография считается одним из самых точных 3D-печатных процессов, причем поверхность объекта, созданного этой техникой, получается высочайшего качества. Среди минусов — необходимость постобработки и то, что со временем объекты становятся более хрупкими.
DLP
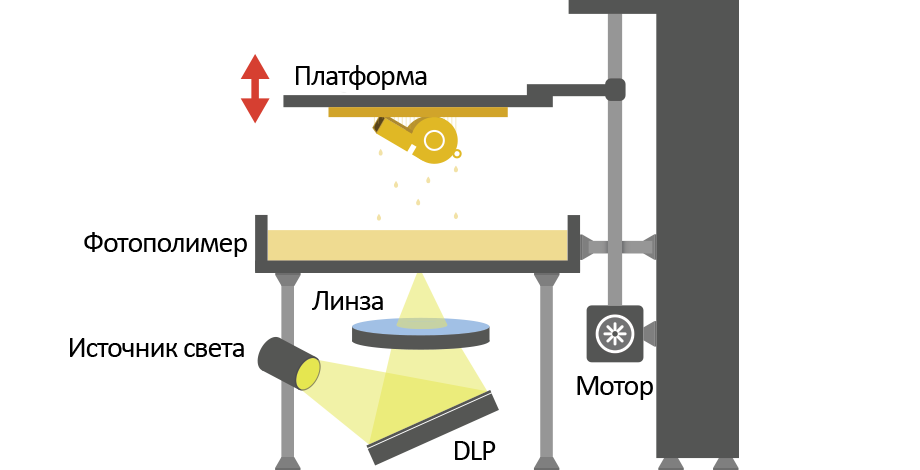
DLP (digital light processing, т.е. «цифровая светодиодная проекция») — это техника, похожая на стереолитографию в том, что в ней тоже используются фотополимеры. Главное отличие — в источнике света. DLP использует более традиционный источник света (вроде дуговой лампы), а также жидко-кристаллическую панель или прибор с деформируемым зеркалом (deformable mirror device или просто DMD), который воздействует сразу на всю поверхность емкости с фотополимером. Как правило, это позволяет создавать объект быстрее, чем при помощи стереолитографии.
Кроме того, как и SL, DLP позволяет делать объекты более высокой точности и с отличным разрешением, но для этой техники требуется и та же постобработка — удаление опор и повторное отверждение. Впрочем, одним из преимуществ DLP по сравнению с SL является то, что для создания объекта требуется лишь одна неглубокая емкость с фотополимером, а это, как правило, позволяет экономить расходный материал.
Лазерное спекание / лазерное плавление / SLS
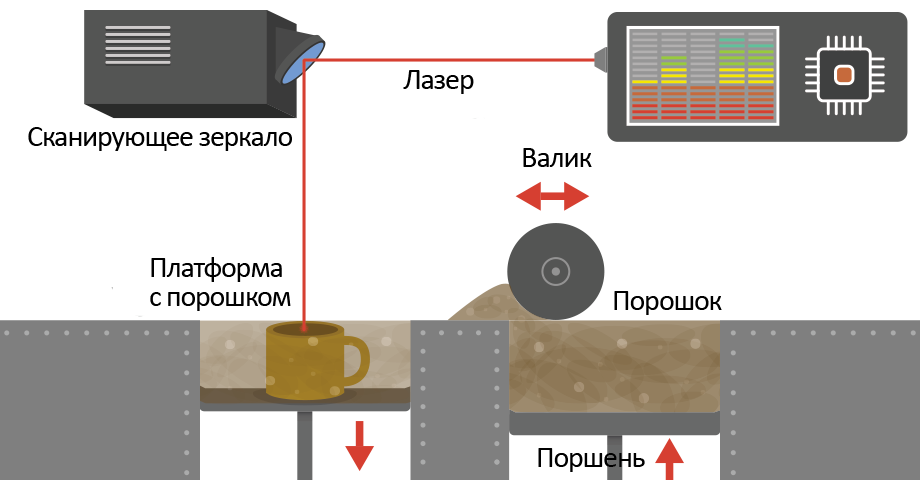
Лазерное спекание и лазерное плавление — это взаимозаменяемые термины, обозначающие 3D-печатный процесс, при котором объект создается путем обработки лазером порошкового материала. В 3D-принтер загружают файл с данными о создаваемом объекте, а лазер, беря за основу эти данные, «скользит» по поверхности исходного материала — порошка, утрамбованного в специальной емкости. Когда лазер взаимодействует с поверхностью, частицы порошкового материала спекаются/сплавляются друг с другом, обретая твердую форму. После создания слоя емкость с порошком опускается на одну ступень вниз, а сверху по ней проезжает валик — он утрамбовывает и подсыпает порошок перед тем, как лазер начнет создавать новый слой, попутно скрепляя его с предыдущим.
Платформа с порошком полностью запечатана, т.к. для успешного спекания необходимо, чтобы исходный материал был определенной температуры. По завершении процесса емкость с порошком вынимается, лишний порошок убирается, и в итоге остается лишь напечатанный объект. Одним из ключевых преимуществ этой техники является то, что порошок служит в качестве опорного элемента для разного рода выступов и свесов, избавляя от необходимости проектировать опоры перед печатью объекта. Следовательно, при помощи лазерного спекания можно создавать сложные объекты, которые невозможно создать при помощи других техник.
Впрочем, у этой техники есть и недостатки — из-за высокой температуры, необходимой для лазерного спекания, очень много времени может понадобиться на охлаждение. Более того, давней проблемой лазерного спекания является пористость на итоговом объекте. И хотя в последнее время на этом фронте видны значительные улучшения, в некоторых случаях для улучшения механических характеристик объекта по-прежнему используют пропитку другим материалом.
При лазерном спекании/плавлении можно использовать пластик и металлы, но сплавление металла требует гораздо более мощного лазера и более высоких температур. Объекты, создаваемые при помощи этого метода, гораздо прочнее, чем создаваемые посредством SL и DLP, но есть и недостатки — более низкие качество поверхности и точность.
Экструзия / FDM / FFF
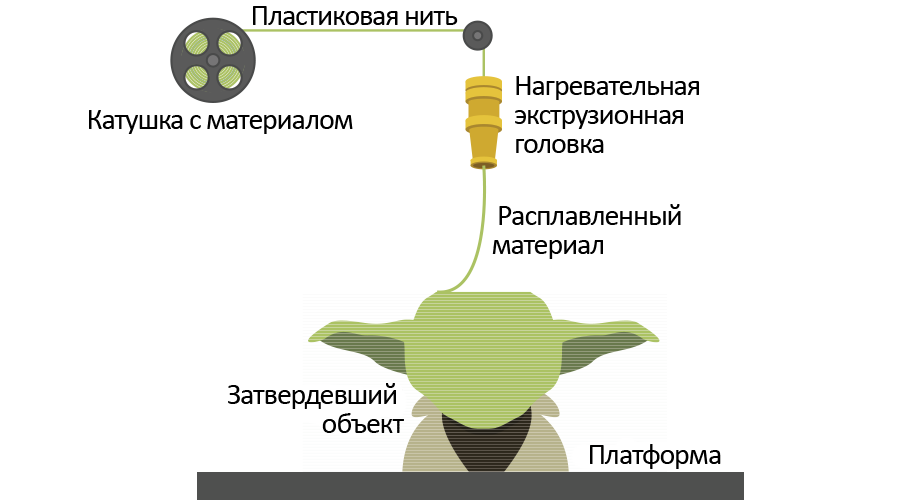
Самым распространенным (и узнаваемым) 3D-печатным процессом является экструзия термопластического материала. Наиболее известное название этой техники — это FDM (т.е. fused deposition modelling или «моделирование методом наплавления»), которое является и коммерческим наименованием, зарегистрированным Stratasys (компанией, которая изначально разработала эту технику). Технология FDM появилась на свет еще в начале 90-ых, но используется и по сей день, причем даже на промышленном уровне. Большая часть 3D-принтеров начального уровня, появившихся после 2009 года, используют похожую технику — она именуется, как правило, freeform fabrication или FFF (что значит «изготовление объектов произвольной формы) и представляет собой упрощенную вариацию FDM, потому что патенты на эту технологию по-прежнему принадлежат Stratasys. Первые RepRap и их последователи — и коммерческие версии, и версии с открытым кодом — тоже используют метод экструзии. Однако после иска о нарушении патента, поданного Stratasys против Afinia, то, как будет развиваться рынок 3D-принтеров начального уровня, теперь под вопросом, т.к. все эти машины теперь под угрозой иска со стороны Stratasys.
Суть техники в следующем: пластиковая нить пропускается через экструдер, где нагревается, а затем размещается на платформе — слой за слоем, согласно 3D-данным в файле, «скормленном» 3D-принтеру. Будучи отложенным, пластик застывает и скрепляется с предыдущим слоем.
Компания Stratasys разработала для FDM несколько фирменных материалов, пригодных для производства объектов на промышленном уровне. Диапазон материалов для 3D-принтеров начального уровня более узок, но продолжает расширяться. Самыми распространенными материалами для начальных FFF-принтеров в данный момент являются ABS и PLA.
Объектам, создаваемым при помощи FDM и FFF, требуются опорные элементы — для свисающих частей. В FDM для этих опор используется еще один, водорастворимый материал, который после завершения печати (относительно легко) смывается водой. Впрочем, опоры можно удалить и вручную, просто отломив их от объекта. Для FFF-принтеров начального уровня опорные структуры (или их недостаточное количество) всегда были проблемой, однако, поскольку устройства эволюционируют, улучшаются и оснащаются двойными экструзионными головками, она становится все менее болезненной.
Что касается создаваемых объектов, FDM от Stratasys – это довольно точный и аккуратный процесс и, к тому же, относительно дружественный к использованию дома и в офисе. Правда, после печати объекта может потребоваться долгая постобработка. Впрочем, как можно ожидать, на начальном уровне (т.е. при использовании FFF) объекты получаются менее точными, но ситуация постоянно улучшается. Если у создаваемого объекта сложная геометрия, то процесс может быть довольно долгим, и сцепление слоев друг с другом тоже может быть проблемой, в результате чего объект не всегда получается водонепроницаемым. Впрочем, эту проблему можно решить, например, при помощи ацетона.
Впрыскивание
Эта 3D-печатная техника бывает двух видов.
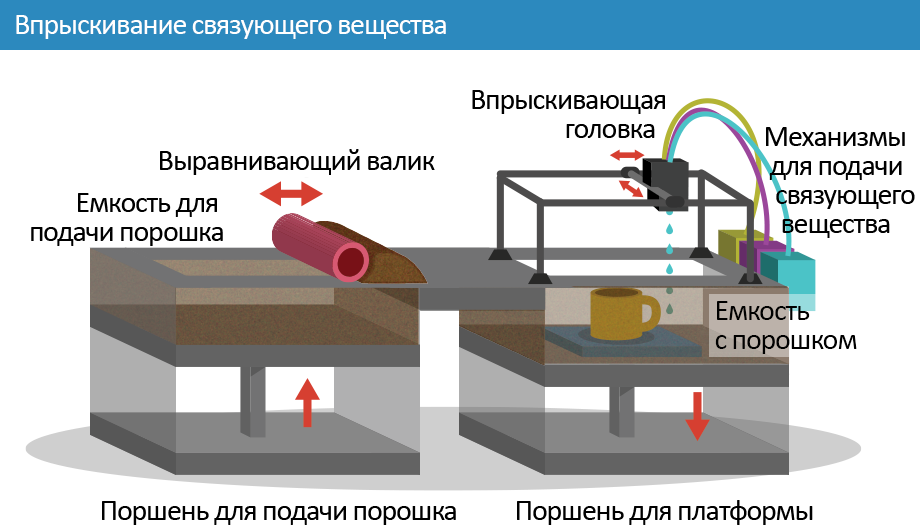
Впрыскивание связующего вещества (binder jetting). В данном случае впрыскиваемым материалом является связующее вещество — оно выборочно впрыскивается на емкость с порошком, чтобы сделать из него один слой. После этого емкость с порошком опускается на ступень ниже, а сверху на по ней пробегает валик (или пластина), который подсыпает в емкость еще порошка, а заодно утрамбовывает его перед следующим проходом впрыскивающей головки. Вещество из этой головки связывает предыдущий и следующий слои друг с другом.
Преимуществом этой техники (как и у SLS) является то, что объекту не нужны опорные элементы, т.к. в их роли выступает порошок. Кроме того, диапазон используемых материалов включает в себя керамику и еду. И еще одно важное преимущество — возможность раскрасить объект разными цветами, что осуществляется через добавление красителя в связующее вещество.
Таким образом, такой 3D-принтер создает практически готовый объект, но он получается не таким прочным, как при лазерном спекании, а для обеспечения долговечности требуется некоторая постобработка.
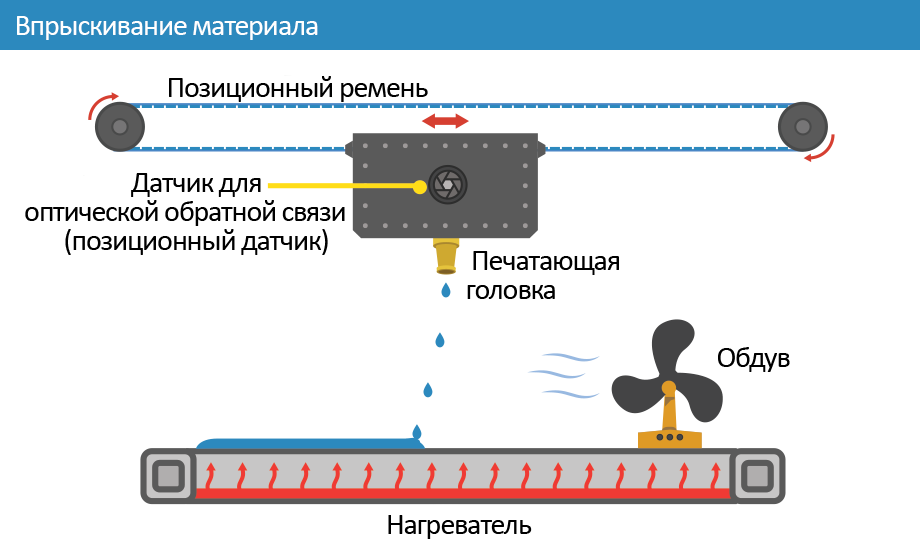
Впрыскивание материала (material jetting). В данном случае впрыскивается, собственно, сам материал (в жидком или расплавленном состоянии) — это происходит выборочно и из нескольких головок (одновременно с другими материалами). Как правило, эта технология использует жидкие фотополимеры, и после наложения нового слоя он подвергается воздействию ультрафиолетового света, благодаря чему отвердевает.
Кроме того, в связи с тем, что этот метод позволяет одновременное использование сразу нескольких материалов, то и объект тоже можно сделать неоднородным — чтобы разные его части имели разные свойства и характеристики. Впрыскивание материала является очень аккуратным методом 3D-печати, позволяющим создавать точные объекты с очень гладкой поверхностью.
Ламинирование методом селективного насаждения (SDL)
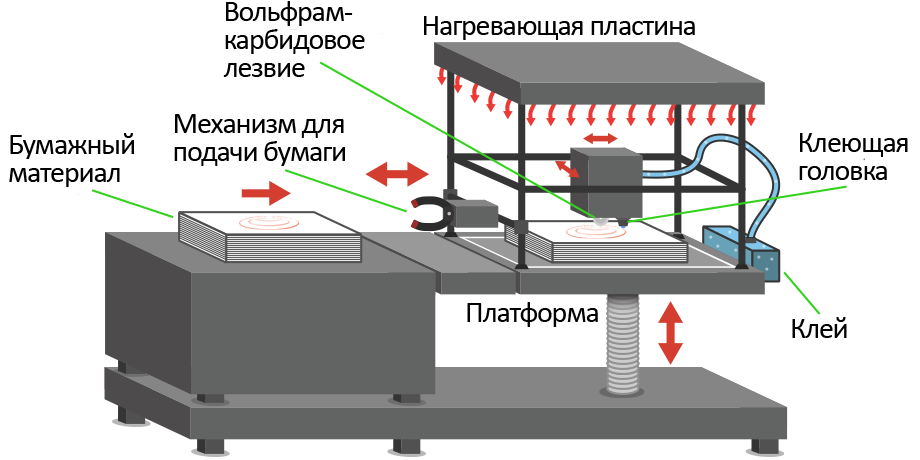
SDL – это 3D-печатная техника, разработанная компанией Mcor Technologies и ею же запатентованная. Есть соблазн сравнить эту технологию с LOM (т.е. с «изготовлением объектов при помощи ламинирования»), которую в 90-ых годах разработала компания Helisys, т.к. оба метода используют бумагу и послойное наложение. Впрочем, на этом сходства между ними заканчиваются.
SDL создает объекты слой за слоем при помощи стандартной копировальной бумаги. Новый слой скрепляется с предыдущим посредством клея, который применяется выборочно в соответствии с 3D-данными из файла, загруженного в принтер. Это значит, что в местах, где будет, собственно, сам объект, клея будет добавляться много, а там, где будут опорные элементы — гораздо меньше, чтобы потом эти опорные элементы было проще удалить.
После того, как механизм подачи бумаги «скармливает» принтеру новый лист и помещает его поверх предыдущего листа с выборочно добавленным клеем, платформа поднимается вверх, к нагревательной пластине, после чего объект подвергается прессованию — оно должно обеспечить крепкую связь между двумя листами бумаги. Затем платформа возвращается к своей изначальной высоте, где карбид-вольфрамовое лезвие пробегается по контуру объекта, тем самым создавая края нового слоя. По завершении резки 3D-принтер накладывает новый слой клея и весь цикл начинается заново.
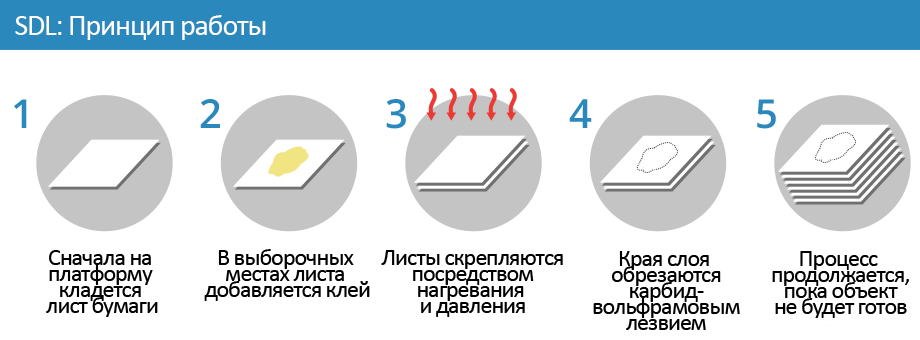
SDL – один из немногих 3D-печатных процессов, использующих палитру CMYK и благодаря этому способных создавать многоцветные объекты. А поскольку исходным материалом выступает обычная бумага, которой не требуется никакая постобработка, эти объекты полностью безопасны и экологически безвредны. Впрочем, по некоторым параметрам SDL все же проигрывает другим 3D-печатным техникам — в создании объектов со сложной геометрией и в том, что размер объектов ограничен размером исходного сырья.
EBM
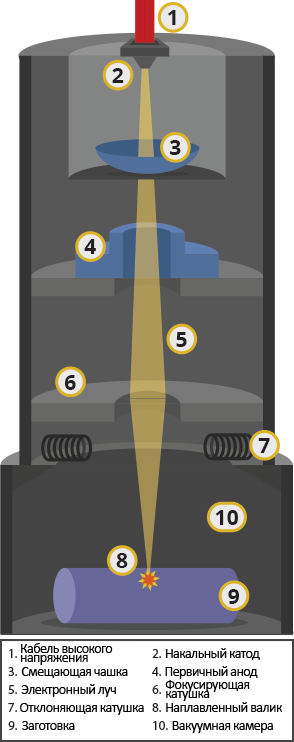
Электронно-лучевая плавка (electron beam melting или EBM) — это 3D-печатная техника, принадлежащая и разработанная шведской компанией Arcam. Она похожа на DMLS (т.е. на прямое лазерное спекание металлов) в том смысле, что обе технологии формируют объект из металлического порошка. Ключевое отличие — в источнике тепла. В технике EBM в его роли, как можно судить из названия, выступает электронный луч, а не лазер, в связи с чем процедура должна проводиться в условиях вакуума.
EBM позволяет создавать изделия максимальной плотности из различных металлических сплавов, в результате чего этот метод успешно используется в медицинской промышленности, особенно для производства имплантов. Тем не менее, другие высокотехнологичные сектора (вроде авиакосмической и автомобильной промышленности) тоже поглядывают в сторону EBM.
См.также
Внешние ссылки