3D-принтер:Заполнение и прочность: Функциональный дизайн за пределами CAD
Содержание | 3D-печать | Материалы для 3D-печати | Хитрости и советы | 3D-модели для 3D-принтера | Программное обеспечение | Неисправности |
Заполнение и прочность: Функциональный дизайн за пределами CAD[1]
Проектирование функциональных объектов, как правило, затрагивает такие вопросы, как прочность и долговечность, которых требуется достичь для печатаемой модели. Если не брать в расчет самого дизайна, дизайнер должен в самую первую очередь беспокоиться о том, каким образом будет проходить процесс печати, включая подбор правильных материалов и параметров.
То есть дизайнер должен задать себе следующие вопросы. Каким методом печатать модель? Каким материалом? Какой тип заполнения использовать? Какой процент заполнения использовать? Какие подобрать значения для толщины стенок, высоты слоя и ширины сопла? Чтобы конечный потребитель получил как можно более функциональную модель, для всех этих вопросов нужно найти как можно более точные ответы. И это приводит нас к следующему вопросу – как сильно на прочность объекта влияют параметры, указываемые в слайсере?
Итак, из этой статьи мы узнаем, во-первых, как параметры infill («заполнение») и shell («стенки») влияют на прочность объекта, во-вторых, как менять эти параметры, чтобы достичь оптимального дизайна печатаемой модели, и в-третьих, почему модели с небольшим заполнением обладают большей гибкостью.
Как влияют на прочность объекта параметры «shell» и «infill»
В этой статье будут приведены некоторые экспериментальные результаты, из которых мы попробуем сделать какие-то более общие выводы. Важно отметить, что конечные форма и применение объекта сильно зависят от того, как на его прочность влияют параметры infill и shell. Поэтому данную статью не стоит рассматривать как руководство к действию – это лишь отправная точка для ваших собственных изысканий. Дизайнер должен сам определить, какие значения подойдут для создаваемой им модели, а какие нет.
Для наших тестов мы использовали стандартную 6-миллиметровую консольную балку, проверяя ее на грузоподъемность при помощи пластикового ведра, ко дну которого приставлена линейка. Хотя этот тестовый «полигон» выглядит довольно грубо, для наших целей (а мы, напомню, намереваемся сделать какие-то более-менее общие заключения) он вполне годится. Впрочем, использовать его для проверки детали под какое-то конкретное применение, разумеется, не стоит.
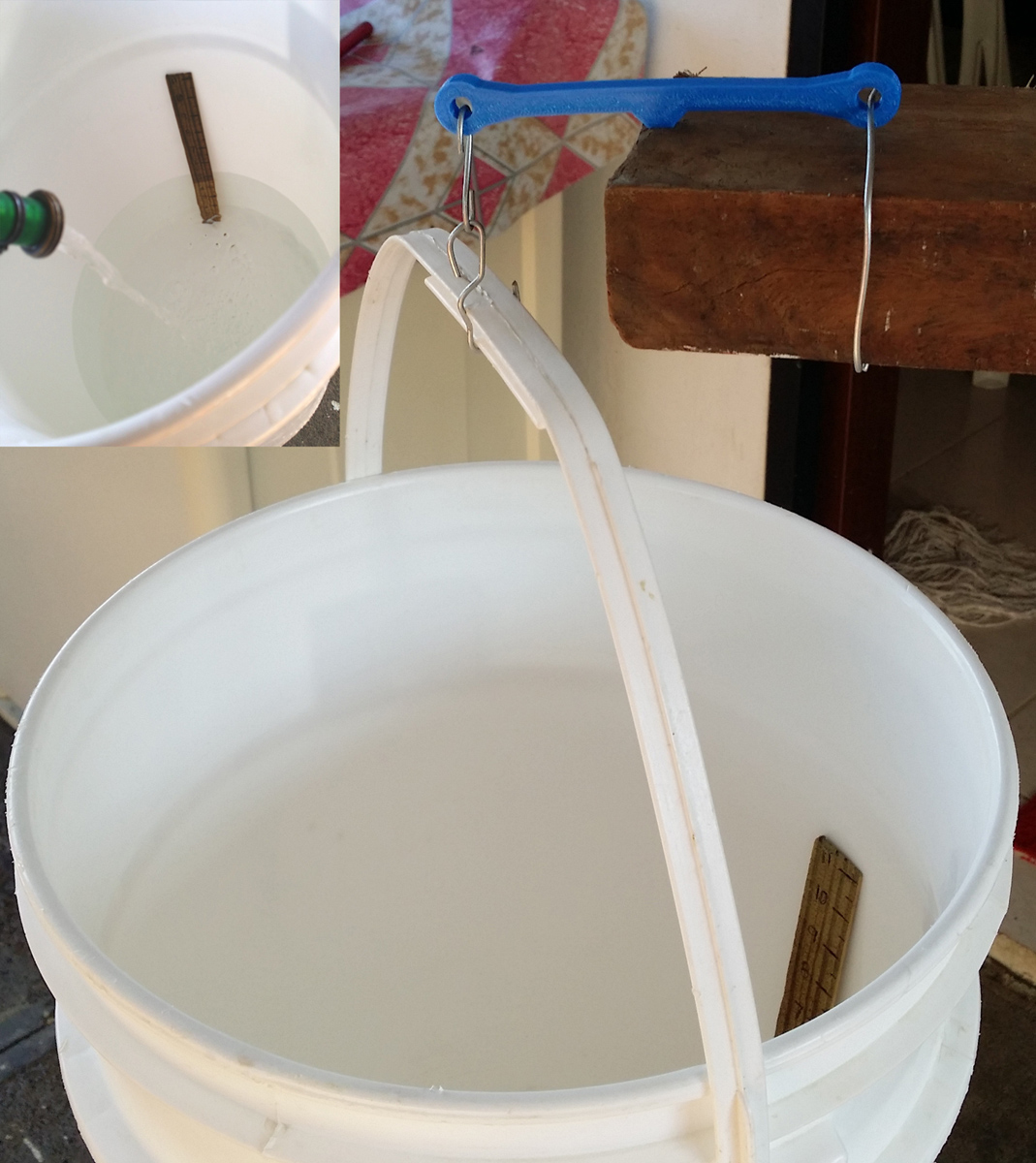
Для нашего теста мы подготовили четыре консольных балки. Все они выполнены из одной и той же модели, но для каждого отдельного случая настройки слайсера были разными. Мы использовали слайсер Cura – он дает хорошие результаты, а для визуализации передвижения печатной головки имеет стильную функцию 3D-просмотра. Параметры были настроены таким образом, чтобы у первых трех балок толщина стенки составляла 0,7 мм, а заполнение (линейным шаблоном, т.е. rectilinear) – соответственно, 25%, 50% и 75%. У четвертой балки толщина стенки была выставлена на 1,05 мм, а заполнение – на 25%.
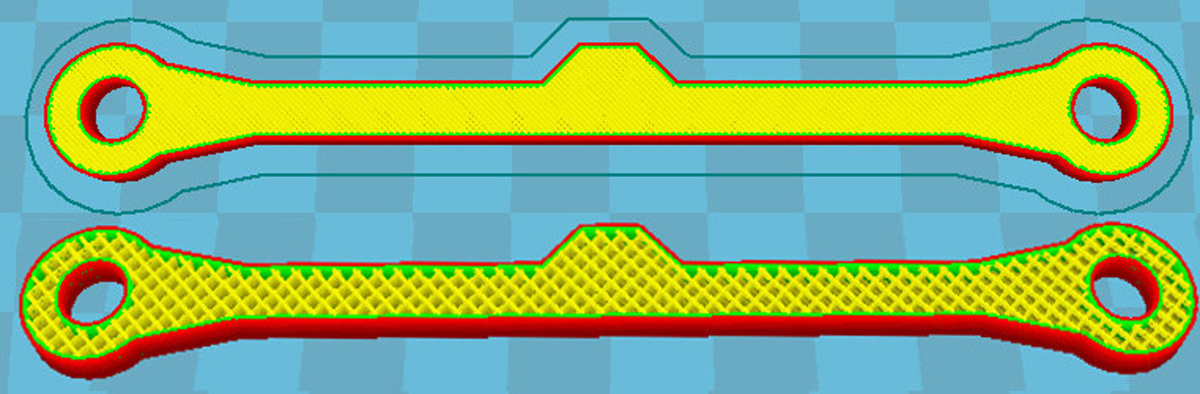
Начинаем испытания
Образцы устанавливались на тестовую площадку следующим образом. Один конец при помощи стальной проволоки крепился к опорному деревянному бруску, а на другой при помощи той же проволоки подвешивалось пластиковое ведро, с помощью которого и создавалась нагрузка на тестовый образец. При этом выступающая центральная часть балки упиралась в край опорного деревянного бруска. Нагрузка увеличивалась путем добавления в ведро воды – до тех пор, пока образец не ломался. Измерения приблизительные, с возможным отклонением в пределах 3 мм. Таким образом, образец постоянно находился под силовым воздействием, а его разрушение всегда начиналось с трещин на верхней части (той, на которую приходилась основная нагрузка), после чего трещины увеличивались, в конце концов достигая нижней части образца (как и ожидалось).
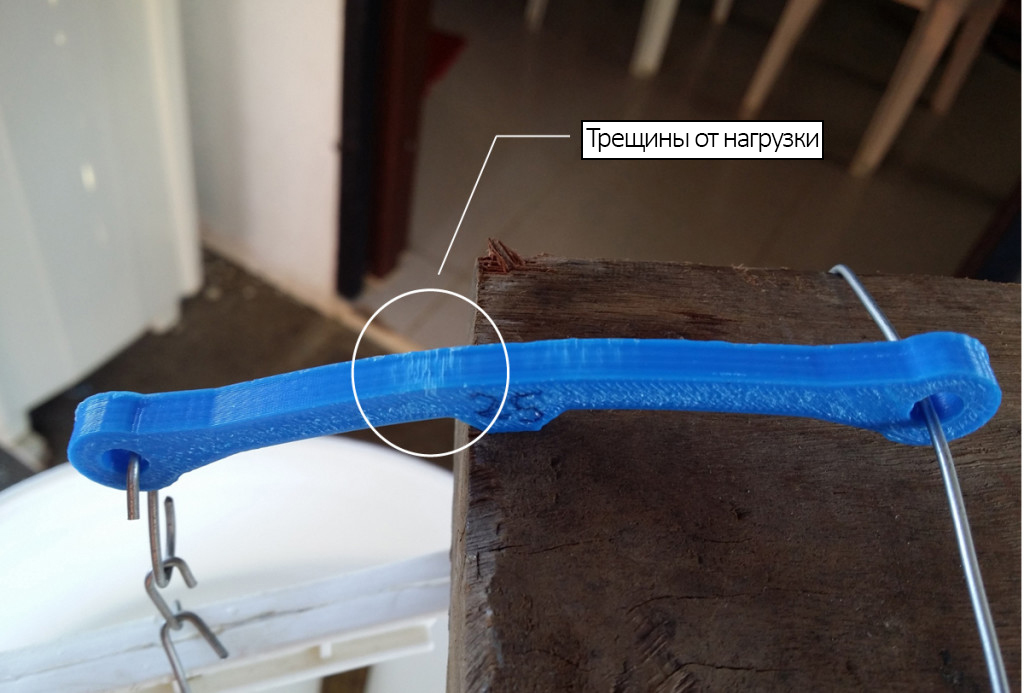
Также стоит отметить, что самый «худой» из тестовых образцов (заполнение – 25%, стенки – 0,7 мм), с одной стороны, показал наихудший результат по грузоподъемности, а с другой, перед тем, как сломаться, сильнее всех изогнулся.
Из этого следует, что при данном типе печатной структуры повышенная прочность достигается в ущерб гибкости и наоборот. Другими словами, чем меньше заполнение, тем гибче становится объект, а чем больше заполнение, тем объект прочнее.
Наибольший прирост в прочности наблюдался между объектами с 25-процентным и 50-процентным заполнением. Прирост между 50% и 75% был хоть и скромнее, но все же остался существенным. Прочность образца со стенками 1,05 мм и заполнением 25% оказалась чуть меньше, чем у образца с 50-процентным заполнением. Филамента тоже потребовалось чуть меньше – 47 см против 51 см.
Процент заполнения/Толщина стенки | Вода в мм | Использованный филамент (3 мм) |
---|---|---|
25% / 0,7 мм | 79,3 мм | 39 см |
50% / 0,7 мм | 107,95 мм | 51 см |
75% / 0,7 мм | 120,65 мм | 63 см |
25% / 1,05 мм | 101,6 мм | 47 мм |
Если посмотреть на график, то у образцов с фиксированной 0,7-миллиметровой стенкой и изменяющимся заполнением наблюдается линейная зависимость между прочностью и использованным филаментом. И это удивительно, поскольку я ожидал, что прочность будет повышаться благодаря утолщению стенок, а не повышению процента заполнения. Почему так вышло – сказать трудно.
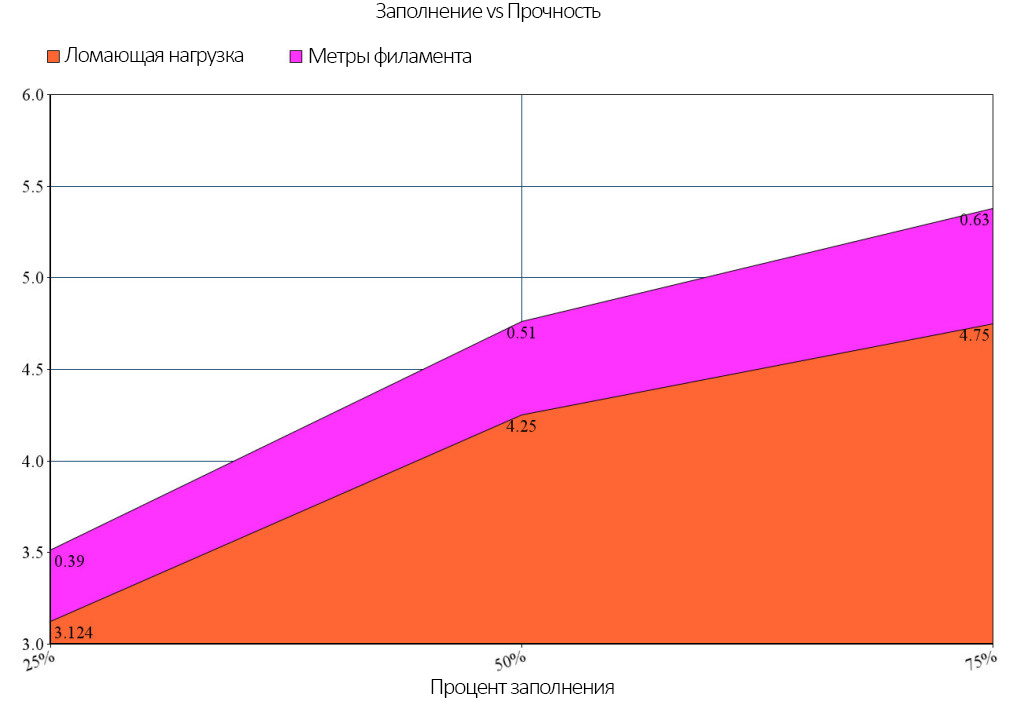
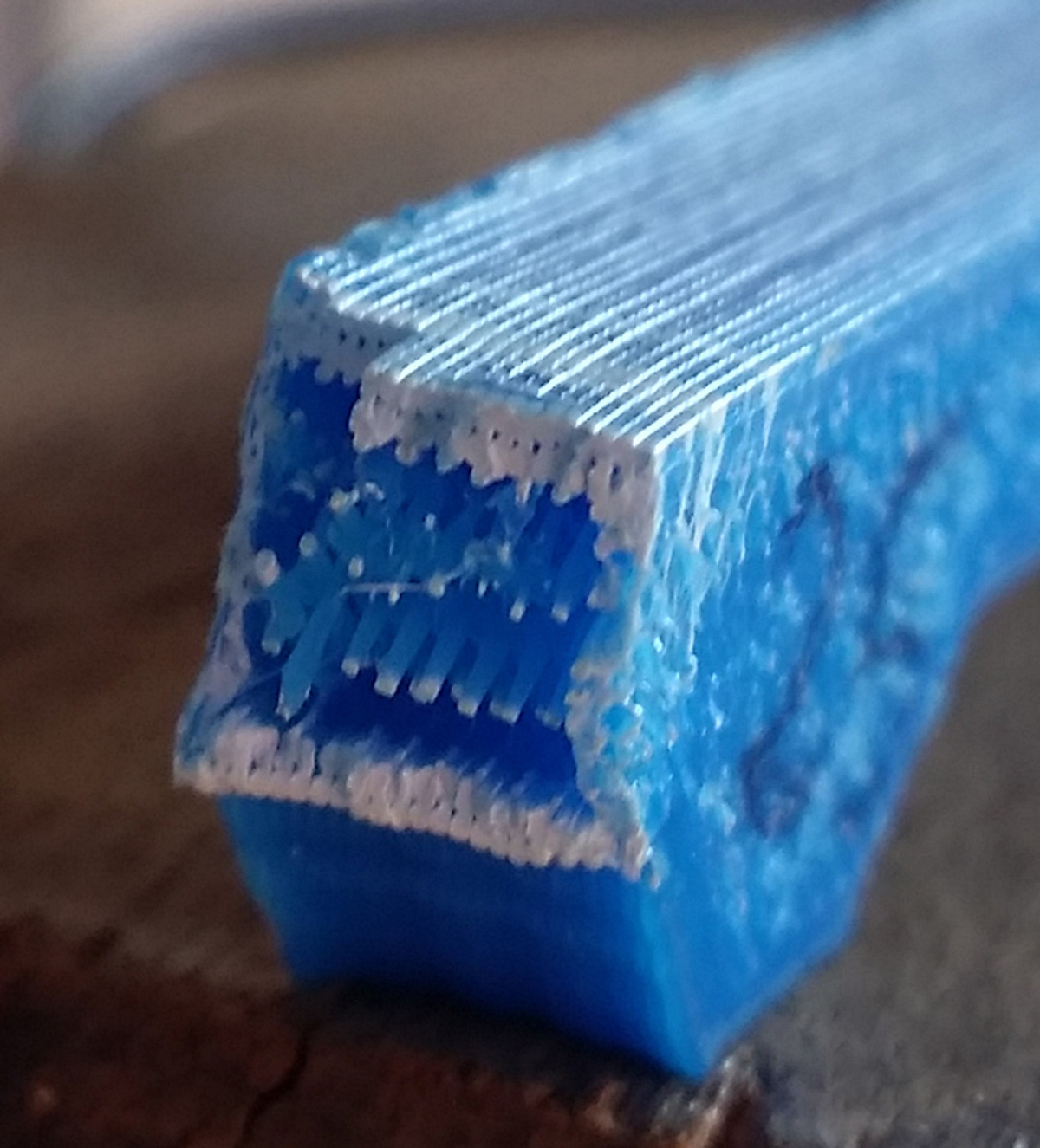
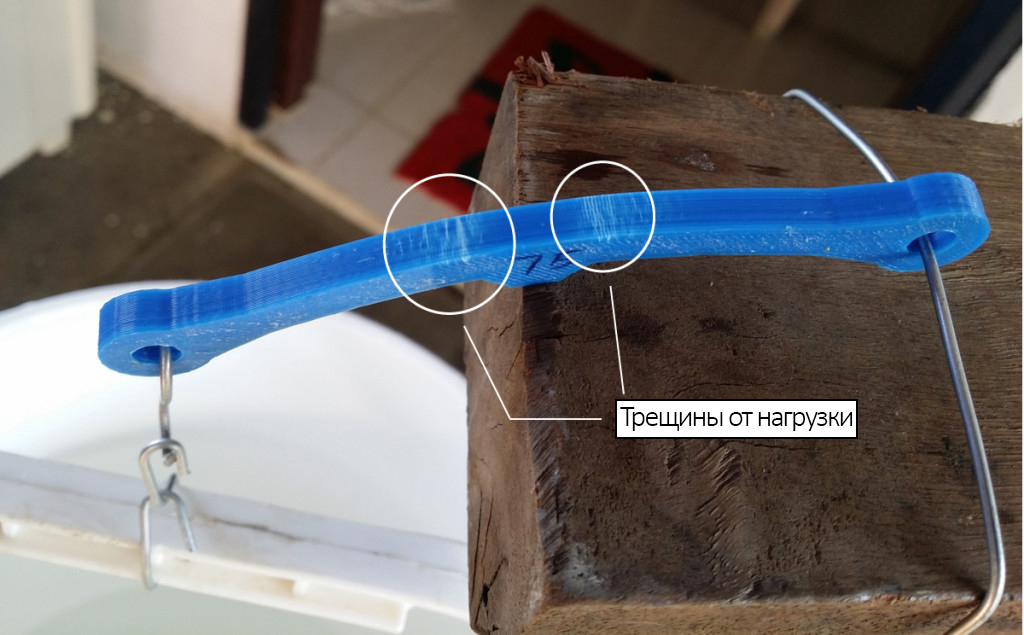
Что мы узнали
Результаты испытаний подтвердили, что более значительный вклад в прочность объекта осуществляется за счет повышения заполнения, и он составляет около 50%. Точка падения эффективности достигнута. Оптимальное заполнение зависит от геометрии модели, шаблона заполнения и ориентации груза. Таким образом, если вашей детали в процессе эксплуатации нужно будет выдерживать нагрузки по оси Z, то она будет более долговечной, если увеличить плотность ее заполнения. Кроме того, интересным наблюдением было то, что образцы с меньшей плотностью заполнения были более гибкими, но с грузоподъемностью у них было хуже.
Среди многообразия методов, которым дизайнер может повлиять на финальную прочность объекта, управление самим процессом печати – наиболее косвенный. В конце концов, пользователь может просто взять где-то STL-объект, отслайсить его, и для каждого отдельного пользователя результаты могут быть очень разными. По этой причине дизайнер должен приложить к STL-файлу с моделью описание, инструкцию или README-файл с информацией о том, какой именно техникой и с какими именно параметрами нужно создавать эту модель.
См.также
развернутьПартнерские ресурсы |
---|
Внешние ссылки