3D-принтер:Материалы для 3D-печати/Как сделать филамент самому
Содержание | 3D-печать | Материалы для 3D-печати | Хитрости и советы | 3D-модели для 3D-принтера | Программное обеспечение | Неисправности |
Как сделать филамент самому[1]
На сегодняшний момент одним из серьезнейших недостатков 3D-печати является высокая стоимость филамента, т.е. 3D-печатного термопластика, который является для вашего 3D-принтера расходным материалом. Безо всяких сомнений, филамент стал гораздо доступнее, чем 2-3 года назад, и ассортимент стал пошире, уже не говоря о разнообразии материалов. Но если цены на 3D-принтеры постоянно снижаются, то цены на филамент за ними как-то не спешат.
В особенной степени это касается филамента высокого качества. Впрочем, конкуренция между производителями филамента в последнее время обострилась, что в дальнейшем должно привести к более массовому производству этого продукта и, следовательно, к его удешевлению, однако на данный момент килограммовая катушка филамента стоит довольно дорого – порядка 22-30 долларов. А если это какой-то особый вид филамента, то за 0,5 кг придется выложить все 50 баксов. И цены такие высокие отчасти по той причине, что производство и продажа филамента – это очень прибыльный бизнес.
Именно тут на сцену выходят так называемые «настольные экструдеры» – машины для производства филамента в домашних условиях. Как это выглядит? Взгляните на фото ниже. Это Noztek Pro, стильный настольный экструдер родом из Великобритании. Давайте попробуем разобраться, как он работает, а потом перейдем к анализу производственного процесса и ценам на сырьевые материалы.
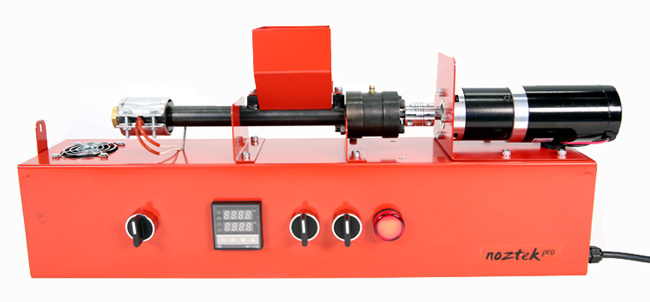
Принцип работы
Общий принцип стандартного настольного экструдера показан на иллюстрации ниже:
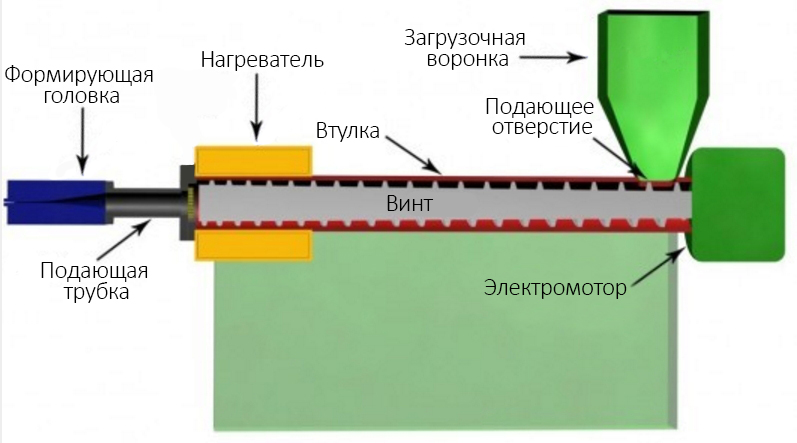
Главная часть экструдера – это втулка, внутри которой находится винт (его также иногда называют «буром» или «сверлом»). На одном из концов винт соединен с нагревателем («нагревательной камерой» или «нагревательным элементом»), а на другом – с электромотором. Мотор приводит винт в действие, тем самым осуществляя транспортировку пластиковых гранул (см. иллюстрацию 9 ниже) через втулку в сторону нагревателя. Сами гранулы подаются во втулку из загрузочной воронки, причем никакого прижимного механизма тут не требуется, т.к. подача материала осуществляется силами гравитации. Таким образом, мотор постоянно крутит винт, а тот перемещает гранулы в сторону нагревателя.
Достигнув его, гранулы нагреваются и начинают плавиться, а полученный жидкий материал выдавливается в сторону формирующей головки. В итоге из нее выходит непрерывная пластиковая нить, чей диаметр соответствует диаметру сопла этой головки. Данный процесс называется «экструзией», поэтому и сам прибор, собственно, называется экструдером. На иллюстрации 3 некоторые из этих частей показаны более подробно.
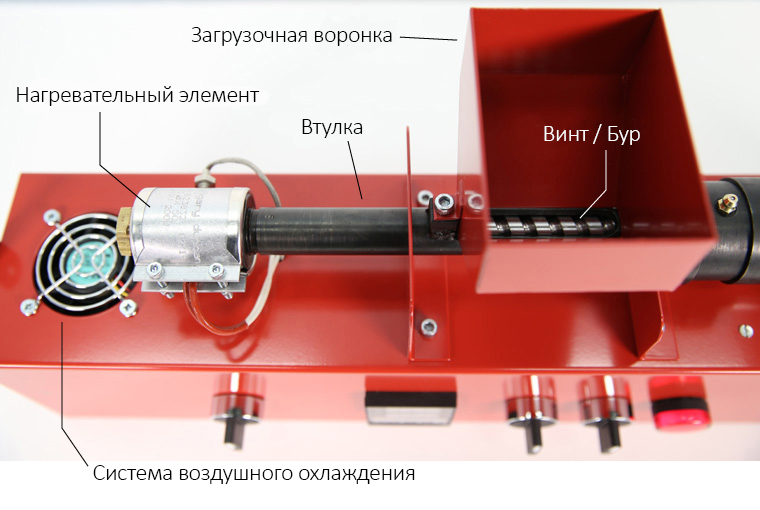
Впрочем, разные модели настольных экструдеров отличаются друг от друга. Некоторые используют большие моторы и шестеренчатый привод, другие – шаговые моторы, которые вращают винт напрямую. Большинство экструдеров поддерживают сменные формирующие головки для двух стандартных размеров 3D-печатного филамента – 1,75 и 3 мм. У некоторых есть охлаждающая система (с использованием вентиляторов), у других – нет. У некоторых есть даже автоматическая система намотки филамента на катушку. В зависимости от электроники некоторые экструдеры поддерживают очень точные температурные настройки, а другие – лишь совсем базовые. Просто взгляните на фото ниже. На них показаны разные виды экструдеров, но, несмотря на внешние различия, принцип их работы примерно один и тот же.
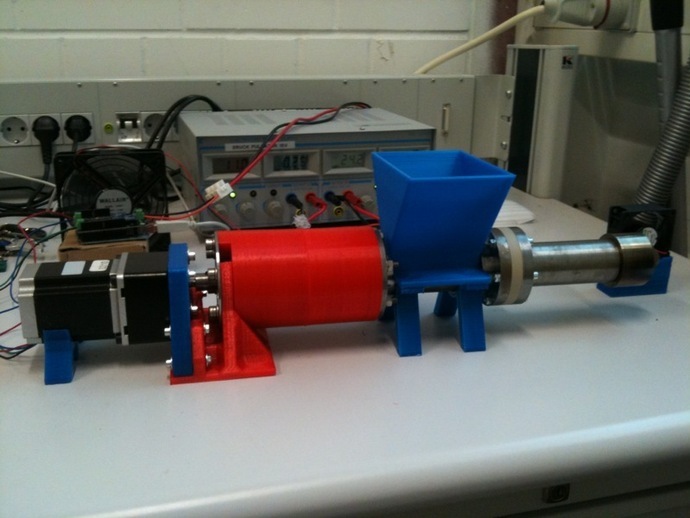
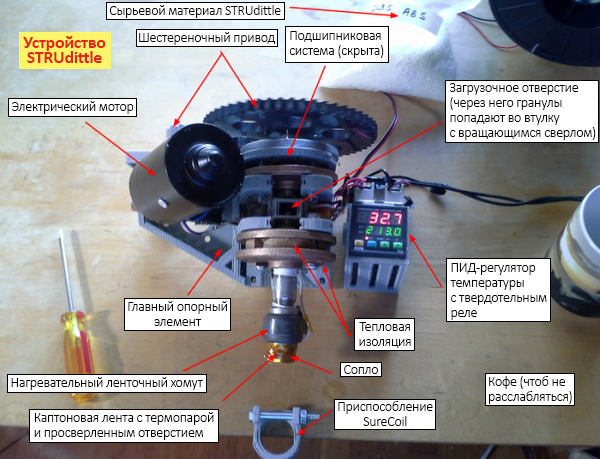
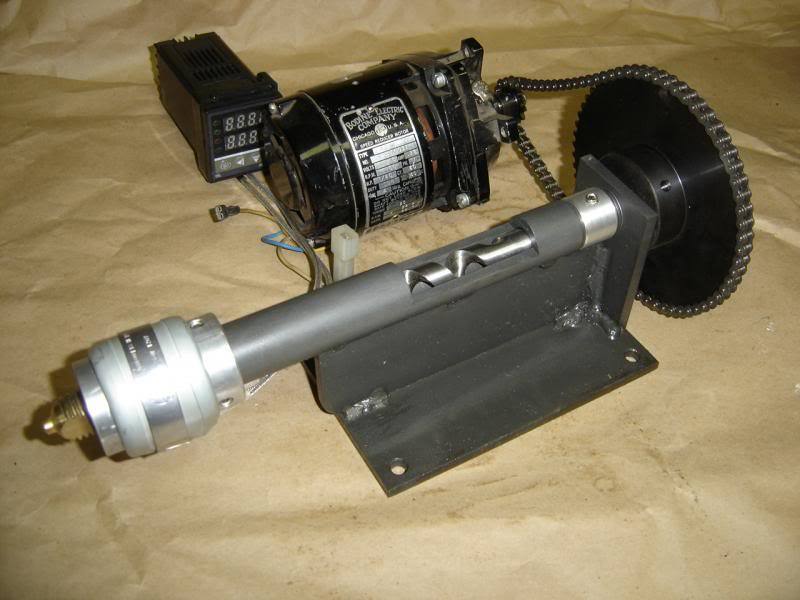
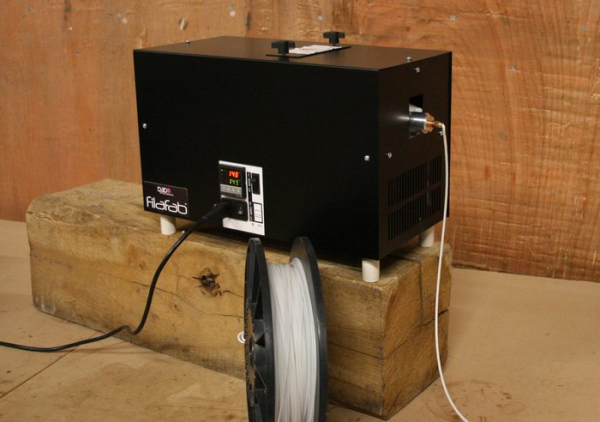
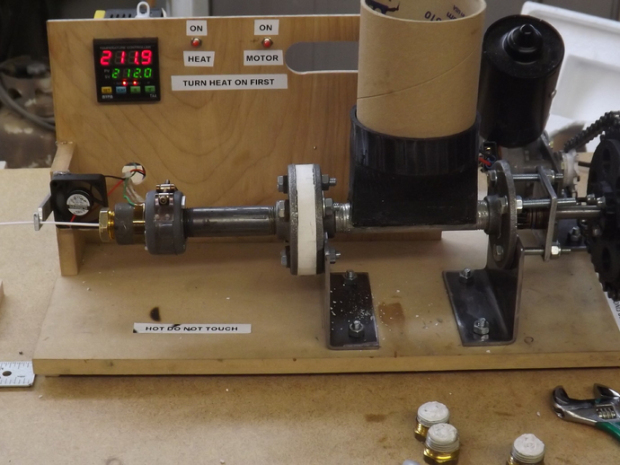
Как видно из фотографий выше, большинство коммерческих машин для настольного производства филамента представляют собой сборные комплекты. Другими словами, пользователю после покупки еще надо будет его собрать. О том, что представляют и как между собой связаны отдельные части экструдера, можно посмотреть на иллюстрации выше, однако, на наш взгляд, будет не лишним показать, как все это выглядит «в реальной жизни».

Теперь, когда мы разобрались в принципе работы экструдера, пора перейти к другим темам.
Сырье
Филамент изготавливается из так называемых «сырьевых гранул». Как они выглядят, можно посмотреть на фото ниже. Стоит отметить, что гранулы на этом фото предназначены для литьевого прессования и сделаны из материалов, которые для 3D-печати могут не подойти. Если не уверены, лучше напишите производителю гранул или оптовику, который занимается их распространением – они должны помочь разобраться вам в этом вопросе.
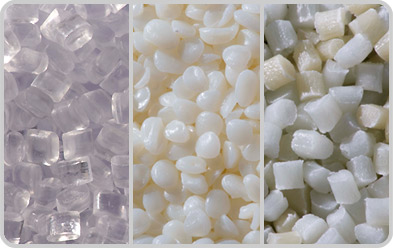
Цвет филамента
Эти сырьевые гранулы, как правило, белые или прозрачные, а их размер составляет всего несколько миллиметров. Эти гранулы смешивают с так называемым «мастербатчем» – это тоже гранулы, которые используются либо для окраски пластика (его называют «цветовым мастербатчем»), либо для придания ему дополнительных свойств (его называет «присадочным мастербатчем»). Цветные мастербатчи – это концентрированные смеси цветовых пигментов, которые в процессе нагревания были преобразованы в смолистое вещество, а затем охлаждены и порезаны до маленьких гранул. То, как они выглядят, можно посмотреть на фото ниже.
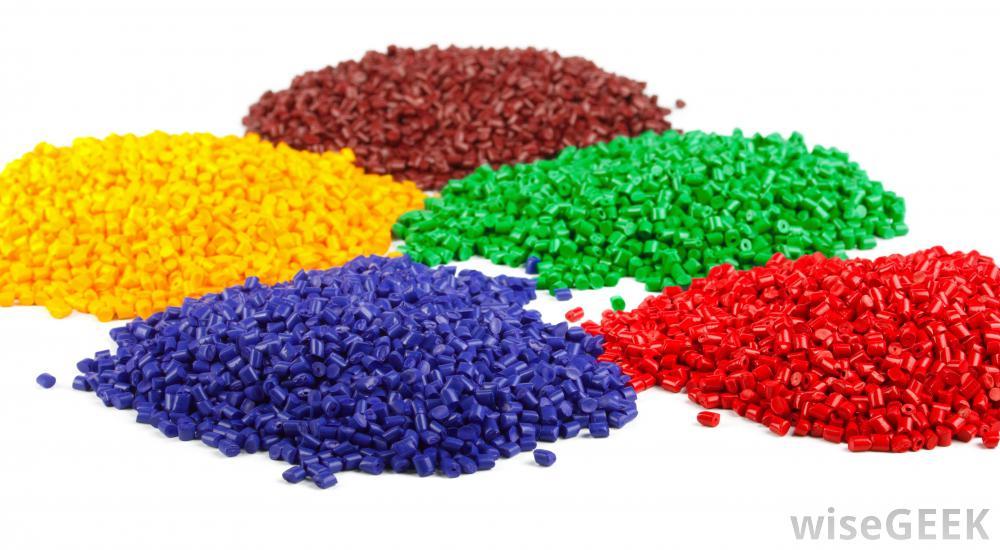
Цветовой мастербатч – это концентрат цветового пигмента, поэтому для придания сырьевым гранулам какого-то цвета к ним нужно добавить лишь совсем немного мастербатча. На фото ниже сырьевые гранулы лежат вперемешку с мастербатчем, чтобы придать филаменту красно-вишневый цвет. На следующем фото показаны разные пропорции сырья и мастербатча, чтобы сделать цвет филамента разным по насыщенности.
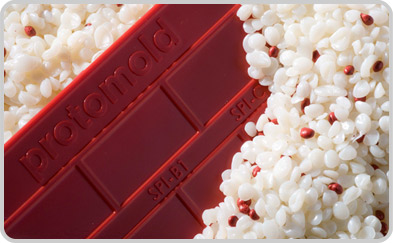
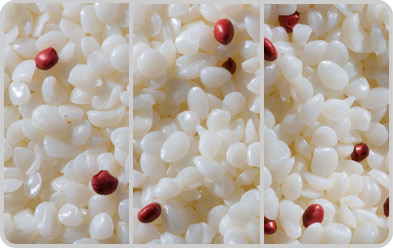
Таким образом, окрашивание филамента происходит путем добавления в него различных цветовых мастербатчей. В то же время вы можете смешивать разные мастербатчи и тем самым создавать какие-то новые цвета. Но перед тем как заниматься этим, обязательно сверьтесь с рекомендациями производителей и погуглите такие понятия как «смешение цветов» и «таблица основных цветов». Кроме того, мы бы порекомендовали провести собственные исследования, записывая пропорции сырья/мастербатча и полученные результаты. Если у вас в итоге получился какой-то приятный цвет или вы нашли материалы, которые хорошо друг с другом смешиваются, имеет смысл поделиться своей находкой с другими людьми, т.к. на данный момент информация об этом довольно скудна.
Почему скудна? Дело в том, что домашнее изготовление филамента – это довольно новая область, однако со временем этой информации должно появляться все больше и больше. Мы определенно посоветовали бы почитать отличный блог Дэвида Смита под названием Bits and Atoms, особенно статьи о смешении и пропорциях мастербатчей. Кроме того, о пропорциях мастербатчей можно почитать, напимер, тут. Примеры различных сочетаний смотрите ниже.
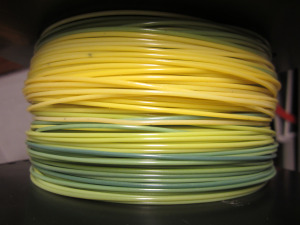
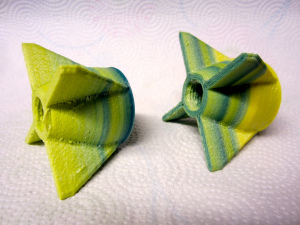
Многоцветный филамент можно изготовить и другим путем – методом Ричарда Хоума (он же RichRap) из richrap.blogspot.com. Ричард использует для этого нейлоновую нить Taulman 618 и при помощи специальных красителей окрашивает ее на манер цветастых хипповских футболок. Впрочем, когда вы просто скармливаете экструдеру гранулы разного цвета, эффект примерно тот же. Кроме того, техника Ричарда слегка замысловата, и для достижения таких результатов вам понадобится ряд дополнительных компонентов. Более подробно можно почитать тут.
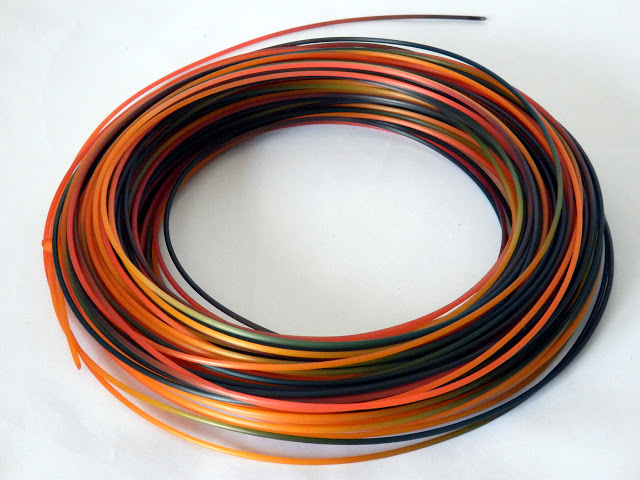
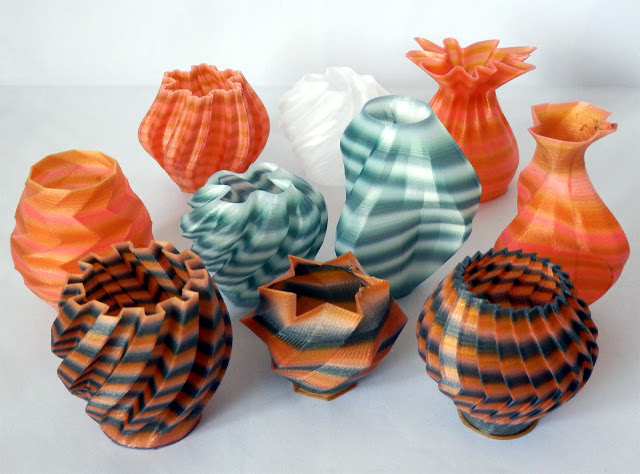
Процесс производства филамента
В промышленном производстве филамента используются, как правило, большие экструзионные линии в виде больших машин, которые способны за одну партию делать сразу несколько прутков (причем без разброса диаметра), что позволяет достичь больших объемов производства. Огромное количество сырьевых гранул нагреваются вместе с определенным количеством мастербатча, причем чтобы добиться цветового постоянства, используются одни и те же пропорции, заранее определенные в научно-исследовательских отделах компаний-производителей филамента. Однако основной принцип промышленного производства филамента почти ничем не отличается от производства домашнего. На иллюстрации ниже показано схематическое изображение этого процесса, а на двух нижеследующих фотографиях – то, как эти конвейерные линии выглядят в реальной жизни.
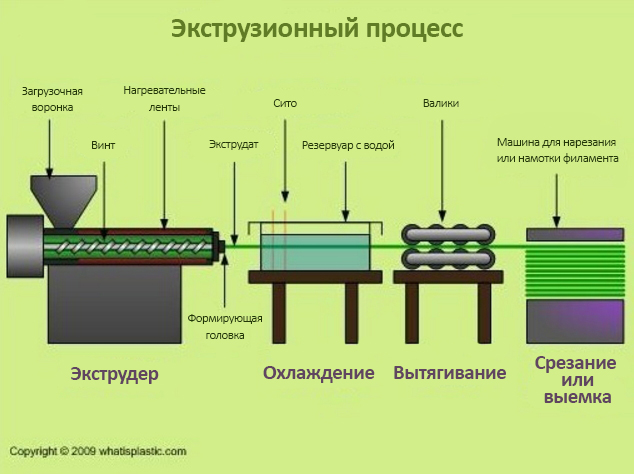
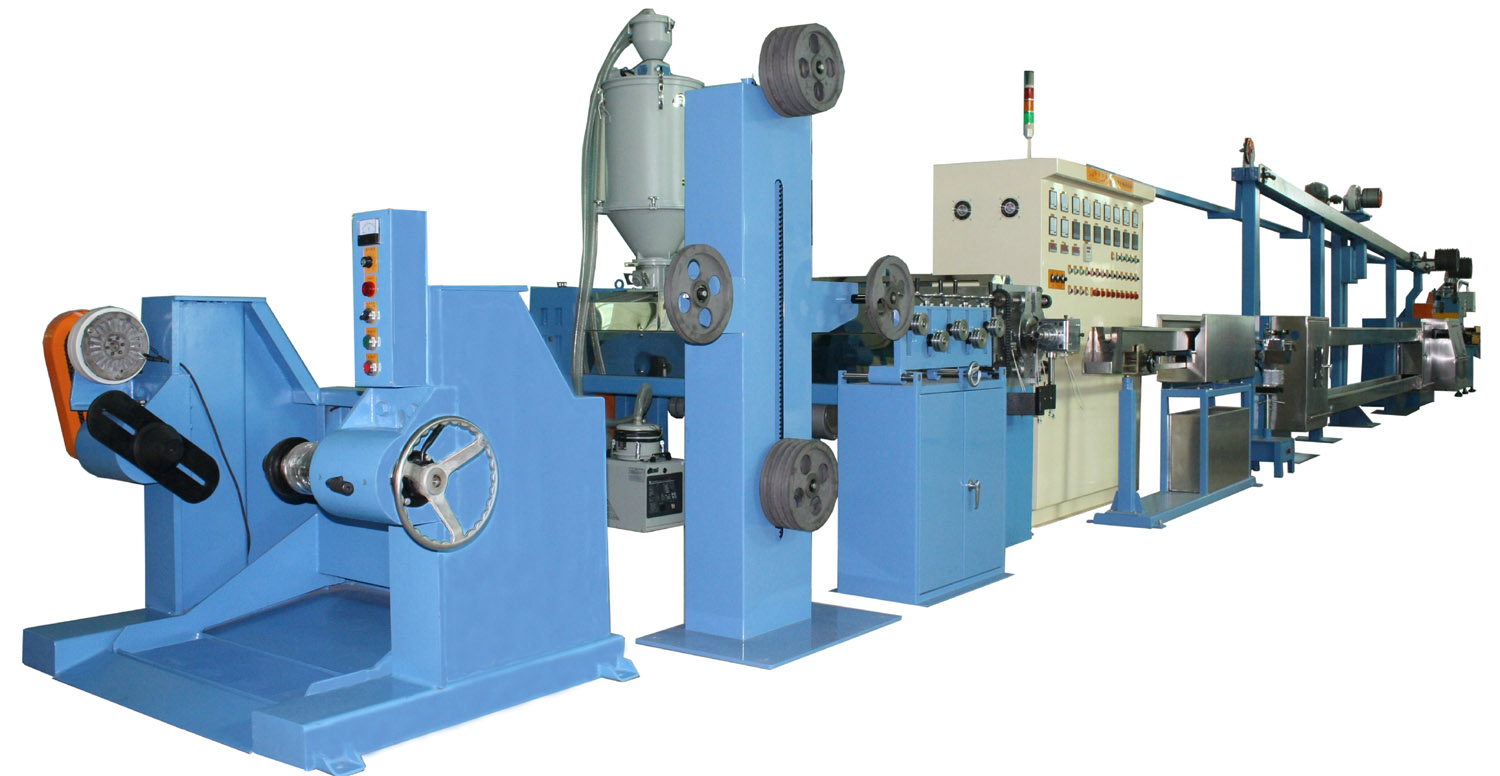
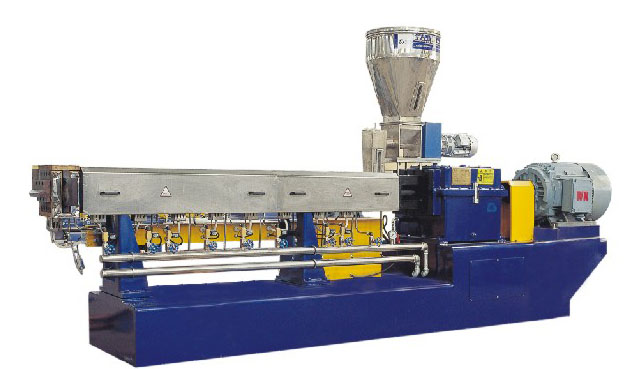
Наиболее значимые отличия – то, что филамент, создаваемый в домашних условиях, не охлаждается сразу после экструзии, и то, что настольный экструдер может экструдировать только один пруток, в связи с чем объемы домашнего производства заметно уступают производству промышленному, где за час можно изготовить несколько сотен килограмм филамента. Кроме того, у домашнего экструдера может не быть специальной машины, которая автоматически наматывала бы экструдированный филамент на катушки. Плюс ко всему, в некоторых случаях эти приборы оборудованы устройством для автоматической проверки диаметра филамента.
Затраты на производство филамента
Однако наиболее животрепещущий вопрос – сколько будет стоить изготовление килограмма кустарного филамента? Начнем с того, что издержки домашнего и промышленного производства по очевидным причинам сравнивать нельзя, поскольку промышленное производство подвергается так называемому «эффекту масштаба», т.е. экономией, обусловленной увеличением масштабов производства. К отдельным людям, которые купили настольные экструдеры для личного пользования, чтобы сделать пару-другую катушек, это правило применить нельзя.
Поэтому цифры, указанные тут, просто ориентировочные, поскольку домашнее производство филамента – это довольно новая область, и розничные торговцы в ней практически не работают. Большинство компаний продают гранулы и мастербатчи оптовикам, и у большинства из них минимальный размер заказа составляет 10-25 кг или больше. Впрочем, в последнее время наметились некоторые подвижки – ряд людей посчитали этот рынок потенциально прибыльным и начали продавать сырьевые материалы в меньших объемах. Впрочем, поиск надежного поставщика, который сумел бы обеспечивать качественный материал в розничных количествах и по приемлемым ценам – это по-прежнему проблема.
На момент написания этой статьи (май 2014 года) килограмм сырьевых гранул стоит примерно от 3,5 до 4 евро. Цветовые мастербатчи стоят примерно от 1,2 до 3,5 евро за килограмм, но их зачастую можно купить лишь в больших объемах (5-10 кг или больше). Но, пожалуйста, помните, что это ориентировочные оптовые цены. Также нужно учесть цены на электричество, стоимость самого экструдера, ее амортизацию, а также различную мелочевку, и в итоге получится, что килограмм филамента стоит около 5-7 евро. Если сравнивать это с розничными ценами, то экономия получается колоссальной – порядка 70%. Правда, перед выходом на самоокупаемость вам придется напечатать довольно много филамента, поскольку экструдеры стоят очень недешево. Список доступных в данный момент настольных экструдеров (вместе с ценами) можно посмотреть в таблице ниже.
Производство филамента из пластикового мусора
Еще одним – зачастую игнорируемым и недооцениваемым – преимуществом владения настольного экструдера является то, что с его помощью можно замкнуть цикл использования пластика. Другими словами, домашний экструдер позволяет переработать не только пластиковый мусор, но и какие-то неудавшиеся (или поломавшиеся, или ставшие ненужными) 3D-печатные объекты. В 2011 году производство пластика по всему миру составило 280 млн тонн (источник)! И хотя меры по переработке пластика с каждым годом становятся все эффективнее, пластиковый мусор все же остается серьезной экологической проблемой – просто взгляните на свалки или эти пластиковые острова, плавающие в мировом океане – поскольку люди выкидывают его сразу после использования.
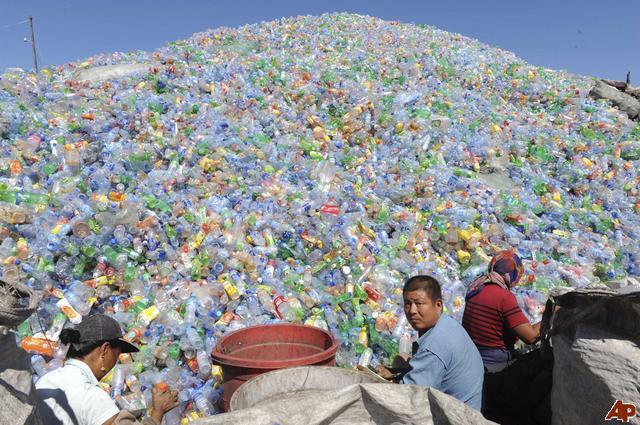
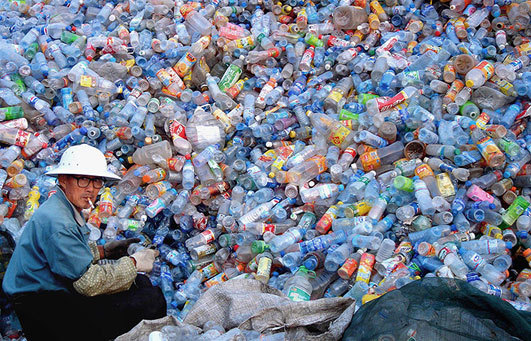
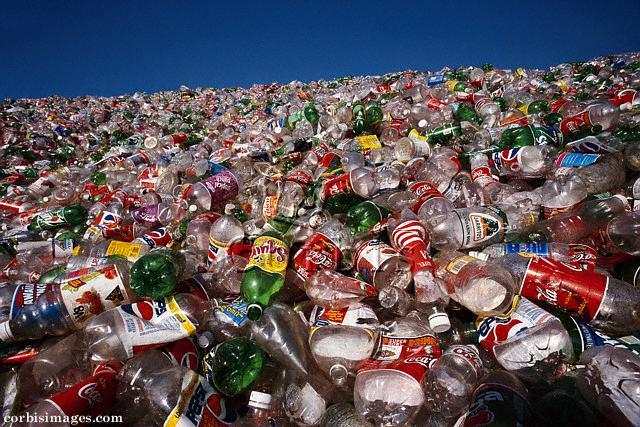
Однако 3D-печать в сочетании с переработкой пластика через экструдеры эту ситуацию может поменять. Нет, мы не хотим сказать, что это изменит мир, но уверены, что это пробьет брешь в бесполезном цикле производства и выкидывания пластика, как только широкие слои населения поймут, что этим «мусором» можно вообще-то воспользоваться для других целей. Возьмем для примера обычную пластиковую молочную бутылку (если в вашем регионе молоко продается не в пластиковых бутылках, просто представьте себе бутылку для воды или флакон для шампуня). Большинство этих бутылок сделано из HDPE, т.е. из полиэтилена повышенной плотности. Они маркируются цифрой «2» в соответствии с идентификационной системой для пластиков.
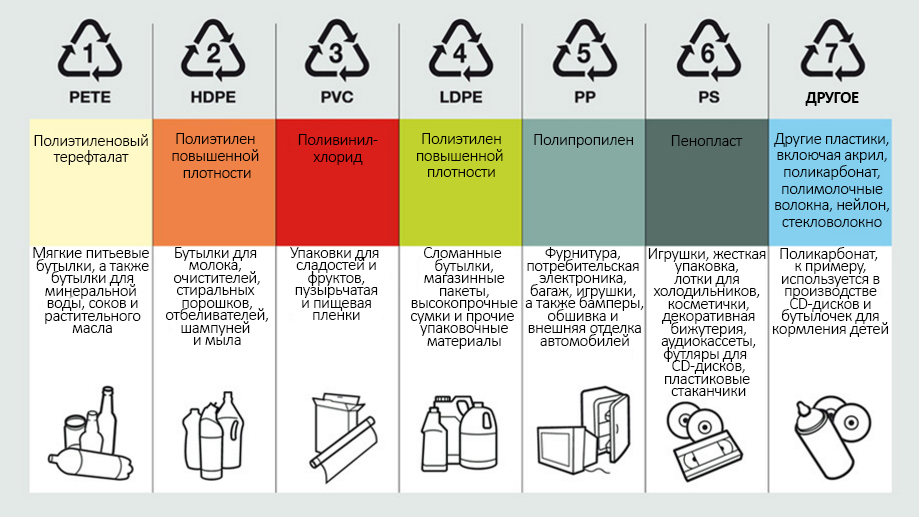
Как правило, эти бутылки выкидываются сразу после использования. Если вас беспокоит состояние окружающей среды, то вы эти бутылки не выкидываете, а утилизируете. Однако если у вас есть собственные настольный экструдер и 3D-принтер, эти бутылки можно сохранить и использовать для изготовления собственного филамента. Хорошо, но как это все работает на практике?
Допустим, у вас есть бутылка с маркировкой HDPE (или PE-HD, или просто с номером «2»). Ее нужно тщательно очистить, чтобы внутри нее не осталось абсолютно никакого содержимого. Теперь удалите все наклейки, ценники и т.д. Затем бутылку нужно порезать на мелкие кусочки и прогнать через измельчитель или тому подобную машину (вроде вот этого самодельного прибора от Маркуса Тимарка), чтобы получившиеся «гранулы» можно было использовать для экструдера. Процесс подготовки пластиковой бутылки показан на иллюстрации ниже.
Как правило, размер получившихся кусочков должен быть 5 х 5 мм – чтобы винт смог протолкнуть их к нагревательной камере. Отклонения должны быть минимальными, поскольку это влияет на вариации в диаметре экструдируемого филамента. После того, как сырье будет нужного размера, его нужно поместить в загрузочную воронку (коническую часть экструдера, куда помещаются гранулы для последующего передвижения по винту). Конечно, весь этот процесс более трудоемок, чем если бы вы просто загрузили в экструдер уже готовые сырьевые гранулы, но его преимущество в том, что полученное сырье получается очень дешевым.
По словам доктора Джошуа Пирсу (Joshua Pierce) из Мичиганского Университета, изготовление филамента при помощи этого метода будет стоить вам всего 0,1 доллара. Огромная экономия по сравнению с покупным филаментом! И добавьте сюда то, что вы используете пластик, который обычно просто выбрасывается. Это открывает новые просторы для использования пластика, который, как выясняется, можно не только вышвырнуть на помойку и тем самым создать проблему для окружающей среды, но и превратить в нечто полезное.
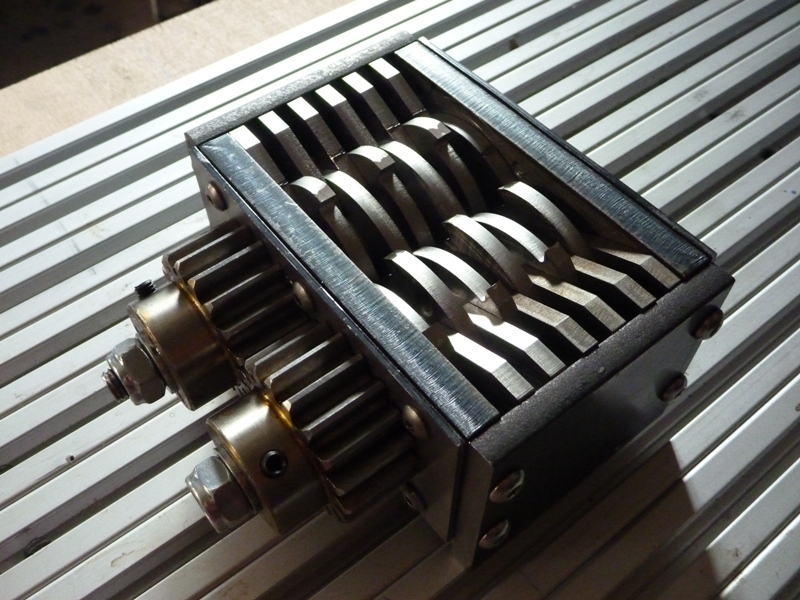
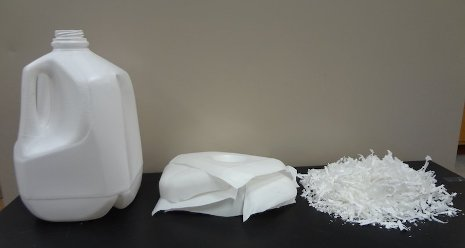
Чтобы осознать потенциал этой технологии, просто взгляните на модель под названием Dremelfuge, напечатанную командой доктора Пирса – для ее создания использовался пластик из выброшенных молочных бутылок. Dremelfuge – это крайне полезная деталь, которая используется в лабораториях в качестве ротора для микроцентрифужных пробирок. Если соединить эту деталь с электроинструментом Dremel, в итоге можно получить полупрофессиональную центрифугу (они используются для выделения ДНК), которая иначе стоила бы вам порядка 300-500 долларов. Более того, Dremel можно раскрутить до 33 тысяч оборотов в минуту, а это значит, что вы можете собрать так называемую «ультра-центрифугу» прямо у себя в гараже.
Это решение, с одной стороны, позволяет людям проводить биологические исследования в домашних условиях без траты кучи денег на дорогое оборудование, особенно если вы не хотите сильно углубляться в это дело. Но есть и более важный момент – в некоторых регионах мира подобные технологии не доступны вообще (из-за высокой стоимости, недостатка инфраструктуры, технологических ограничений и т.д.), в связи с чем подобные самопальные приборы для исследования ДНК приходятся весьма кстати. Просто прикиньте возможности, открывающиеся развивающимся странам, которые зачастую просто утопают в горах пластикового мусора.
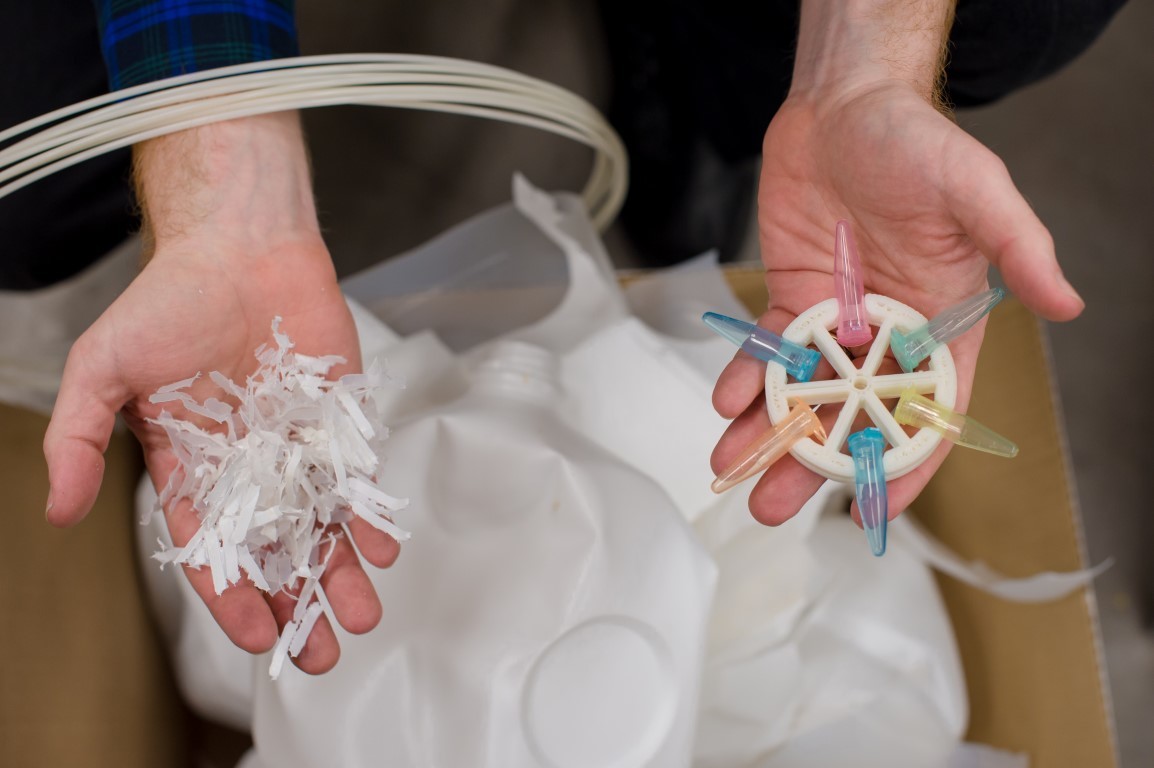
Таким образом, перспективы повторного использования мусорного пластика представляются в еще более интересном свете, даже несмотря на то, что мы находимся лишь у самого истока развития этой удивительной разработки. В то же время переработка пластика и печать с его помощью – это непростой процесс, который по-прежнему требует много ручной работы. Другими словами, данная технология еще далека от идеала. К примеру, 3D-печать с помощью HDPE чревата выгибаниями, поэтому требует нагревательной платформы или даже того, чтобы у принтера была закрытая рабочая камера (для аккумуляции тепла).
Кроме того, важно понимать, что пластик нельзя перерабатывать снова и снова, т.к. он становится хрупким и, если его много раз нагревали, начинает проявлять структурные проблемы. Поэтому за каждой деталью нужно вести, так сказать, «нагревательный дневник», т.к. каждый нагревательный цикл разрушает полимерные цепи, которые, собственно, и образуют, термопластиковый материал. В связи с этим при каждой новой экструзии рекомендуется добавлять к старому сырью какую-то часть новых гранул или измельченного пластика – чтобы материал оставался прочным. Другой момент – всевозможные загрязнители вроде пыли, грязи и чужеродных материалов, которые могут попасть в филамент во время экструзии. По этой причине хороший экструдер должен всегда быть оснащен соплом, в которое встроен специальный фильтр, представляющий собой кусок очень тонкой проволочной сетки. Кроме того, это позволяет избежать закупоривания хот-эндов у принтеров – проблема, исправление которой может обойтись довольно дорого.
Кроме того, в нашем случае речь о переработке именно HDPE-пластиков, однако для домашнего производства филамента можно использовать и другие полимеры. Но тут нужно быть осторожнее, поскольку некоторые пластики (вроде PVC и других полимеров на базе хлорина) могут выделять опасные газы, которые могут серьезно повредить здоровью. Поэтому, экспериментируя с экструзией из мусорного пластика, нужно быть твердо уверенным в том, что вы делаете. Обязательно прочтите данные о безопасности используемого материала!
Список экструдеров
На данный момент доступно лишь несколько экструдеров для домашнего использования. Мы скомпоновали их в короткий список, заодно указав несколько важных характеристик.
Экструдер | Скорость экструзии | Напряжение | Существование и наличие сменных головок и фильтра | Цельный или сборный | Цена |
---|---|---|---|---|---|
Noztek Pro | 1 кг – 3-4 часа | 110В и 220В |
|
Сборный |
1164$ |
FilaFab | Нет сведений | 220В |
|
Сборный | 1170$ |
Filamaker | Нет сведений | Нет сведений | Нет сведений | Цельный | 1655$ |
FilaBot Original | 300 м/ч | 110В и 220В |
|
Сборный | 899$ |
Filabot Wee Kit | 150 м/ч | 110В и 220В |
|
Цельный | 649$ |
FilaBot Wee Assembled | 150 м/ч | 110В и 220В |
|
Сборный | 749$ |
Filastruder | 1 кг – 12 часов | 110В и 220В |
|
Цельный | 299$ |
Lyman filament extruder (DIY) | Нет сведений | Нет сведений | Нет сведений | Нужно собирать самому | 499-900$ |
Extrusion Bot | 120 м/ч | Нет сведений | Нет сведений | Сборный | 625$ |
Что касается скорости экструзии, то производители указывают ее в двух единицах измерения – либо в килограммах в час, либо в метрах в час. Чтобы было наглядней, можно считать, что одна килограммовая катушка 3-миллиметрового PLA-пластика содержит около 110 метров, а килограммовая катушка 3-миллиметрового ABS-пластика – около 130 метров филамента. Если говорить об 1,75-миллиметровом филаменте, то для PLA это будет около 330 метров, а для ABS – около 400 метров. Впрочем, эти цифры могут варьироваться в зависимости от плотности используемого филамента.
Впрочем, есть один экструдер, который выделяется изо всей этой компании сильнее всего – Noztek Pro. Он поставляется уже собранным, это один из самых дешевых экструдеров в своем классе, у него есть сменные головки, фильтр, охлаждающий механизм (со встроенным вентилятором) и планетарный мотор с высоким показателем крутящего момента. При этом согласно Noztek, отклонение в толщине филамента составляет около 0,04 мм, а скорость экструзии – 1 кг за 3-4 часа. И еще специальный бонус – в комплекте с экструдером идет 500 грамм ABS-гранул.
Noztek Pro предназначен для экструзии ABS и PLA, но по словам представителей компании, экструдировать из HDPE – тоже не проблема. Он не только плавится при температуре 180°C, но и позволяет изготовить качественный филамент, причем используя для этого пластик, который обычно просто выкидывается. Кроме того, цвета тоже смешиваются довольно хорошо. Что насчет газов, то по заявлениям Noztek, их источается не больше, чем при работе 3D-принтера. Однако компания все же рекомендует использовать экструдер в хорошо проветриваемом помещении. Ни измельчителя, ни устройства для намотки филамента в комплекте не идет.
См.также
развернутьПартнерские ресурсы |
---|
Внешние ссылки